Why choose a full-service chemical etching partner?
Chemical metal etching is a highly accurate machining process for producing precision metal components with incredibly tight tolerances. Chemical etching is sometimes known as photo chemical milling, photo chemical etching, metal etching, acid metal etching or ferric chloride etching. The range of metals possible is vast, from brass, copper, beryllium copper, to ferrous metals including stainless steel, carbon steel and mild steel, up to a thickness of 1.5mm.
Key advantages of chemical etching
In comparison to common fabrication processes like stamping & laser cutting, chemical etching has no hard tooling costs or lengthy production delays. It also offers no burring, no stress, or material structural changes whilst adhering to the same accuracy tolerances. Chemical etching is an ideal process for electronics, automotive, aerospace and many other critical applications.
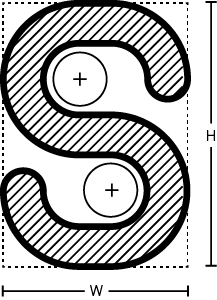
SPEED
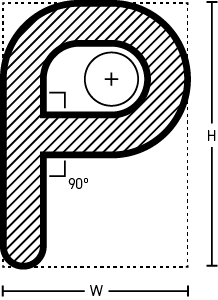
PRECISION
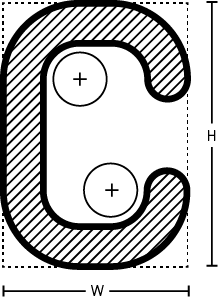
COST-EFFECTIVE
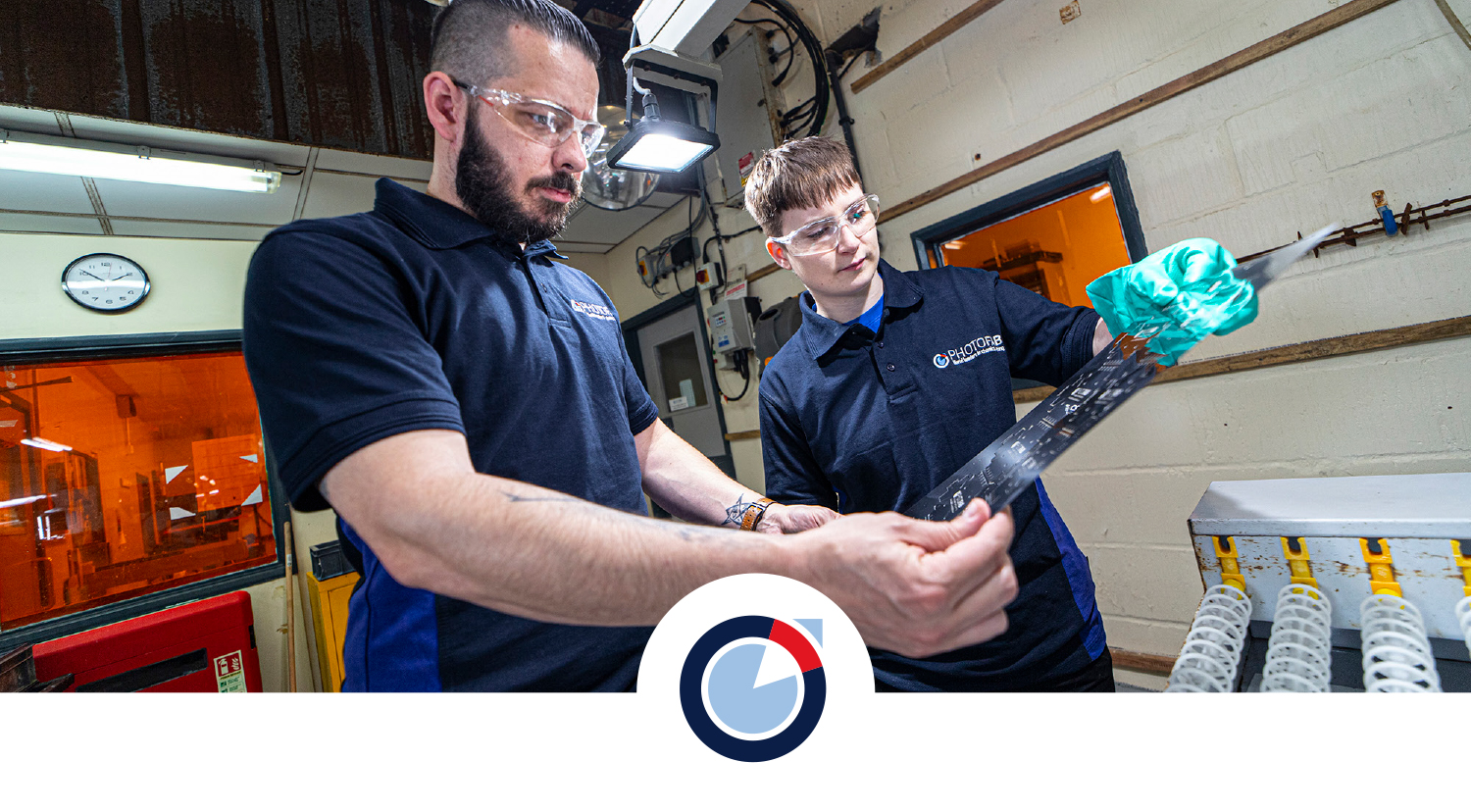
From prototyping to full volume
We understand that quality, speed, and cost are the 3 critical drivers of successful prototyping. Our success in the field arises from a deep understanding of these elements and how to achieve them. For projects that require ongoing high volumes, we offer automation and 24-hour production, all maintained to exacting standards. Combine this with our extensive and trusted manufacturing partnerships, we can offer a multitude of quality manufacturing services to meet your requirements.
What materials can be etched?
We offer an extensive range of metal types and thicknesses, all with full traceability. Various hardness are also offered to meet your requirements. Metal stocks are kept at levels that enable Photofab to offer rapid service to meet the needs of this fact paced industry.

Stainless Steels
Austenitic (301, 302, 304, 316, S526, S527), Martensitic (321, 410, 420), Precipitation Hardened (17/7), Heat Resisting (309, 310)

Other Steels
Mild Steel, Carbon Steel, Tool Steel, Spring Steel, Transil, Losil.

Nickel Alloys
Nichrome, Mu Metal, Nickel Copper (70/30), Inconel, Nickel Brazing Foil.

Nickel/Iron Alloys
Invar, Alloy 42, Kovar, Radio Metal.

Copper
Tough Pitch 101, Oxygen free – High Conductivity.

Copper Alloys
Brass, Phosphor Bronze, Beryllium Copper, Nickel Silver, Ferry Constantan.

Aluminium and Aluminium Alloys

Silver and Alloys
Silver, Silver Alloys, Silver/Copper, Silver/Palladium, Silver Brazing Alloys.
Our chemical etching process
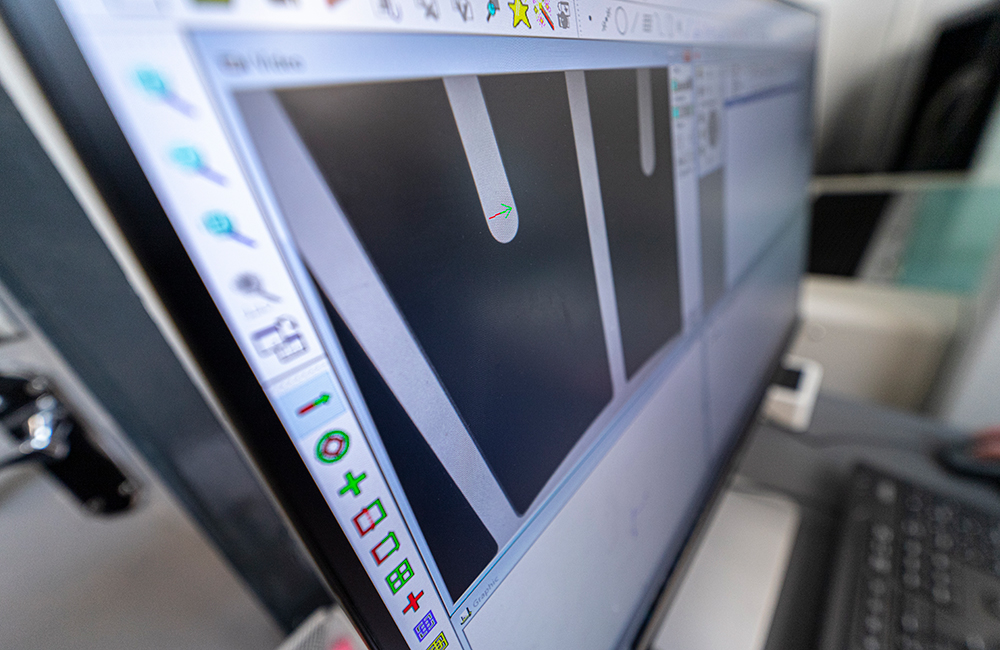
1. Design Advice
At all stages of the chemical etching process, our engineers will offer advice both to improve the product and reduce the costs. We are able to view all types of data; from sophisticated CAD files to rough sketches. Our metallurgist will advise you on the most suitable metal to use for your application. A wide range of metals and thicknesses are held in stock.
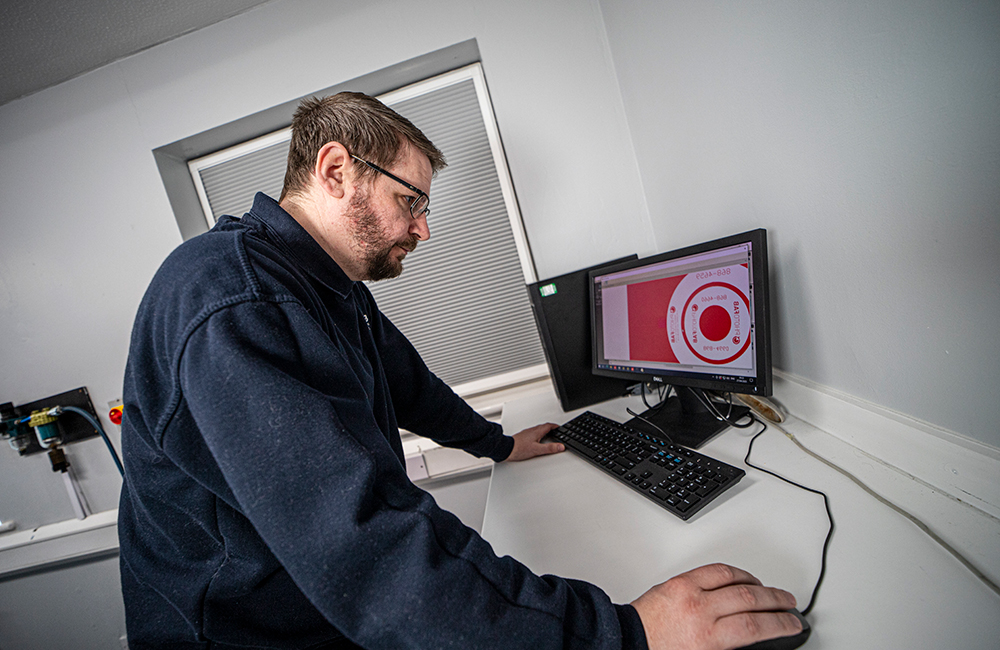
2. Receipt of Drawings
The customer sends data either in the form of a drawing or an electronic file. This is converted using CAD to allow for the etching compensation and “stepped and repeated” to fit as many components as possible onto the film.
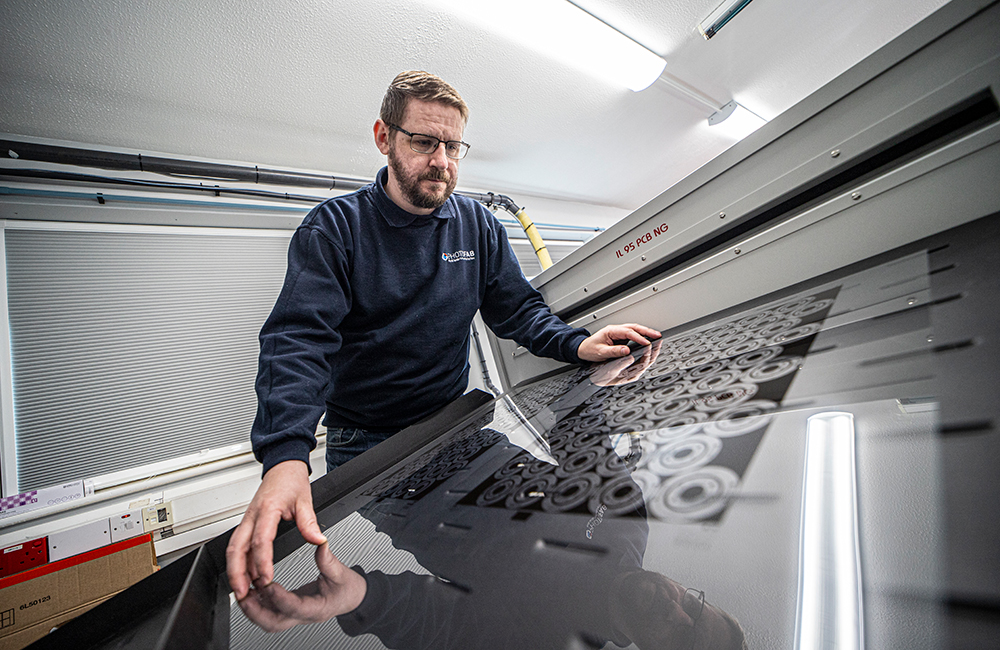
3. Film Plotting
This is then laser plotted to create the Graphic Tool. Two tools are prepared; one for each side of the metal, which allows etching from both sides. Variances between the two tools can facilitate “half-etching” from one side.
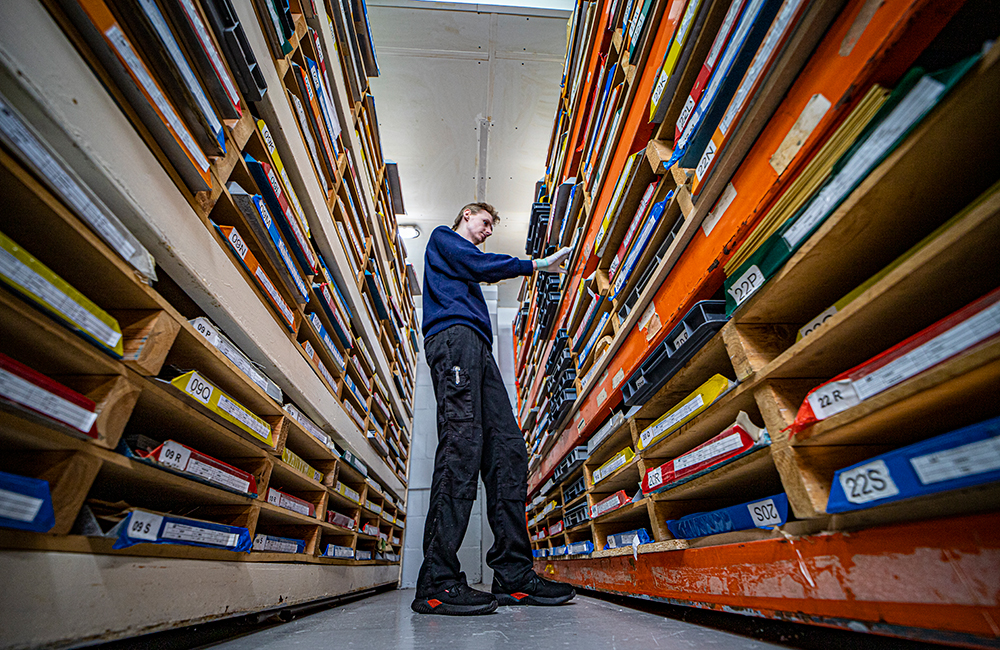
4. Metal Selection
We carefully review your drawing to ensure that the correct metal has been selected both from a performance and cost perspective. Full traceability is maintained on all grades of metal, certificates are available upon request.
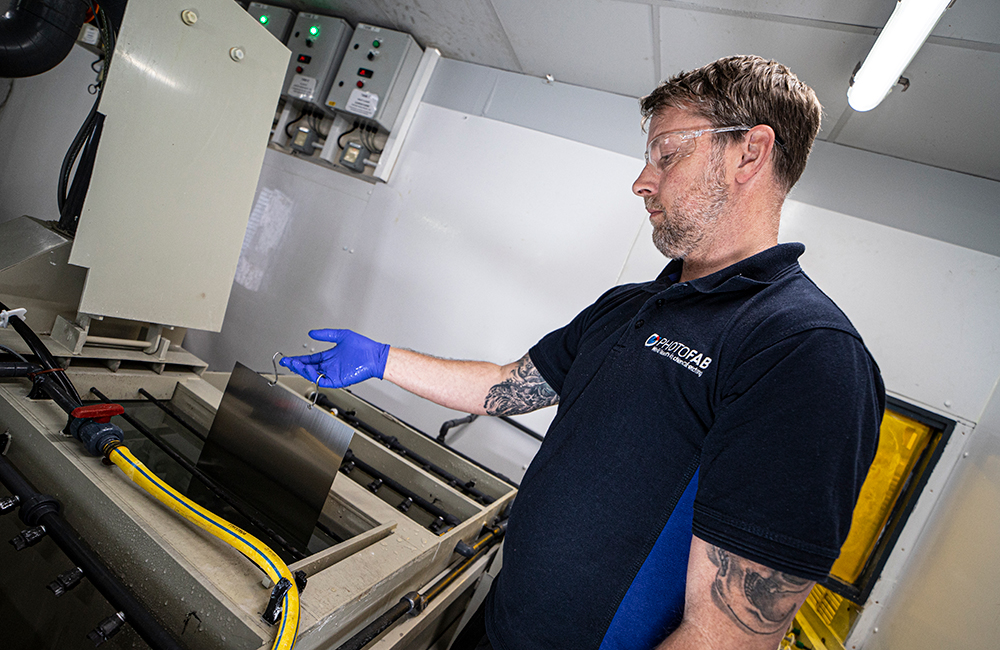
5. Metal Preparation
Before coating the metal with a photosensitive resist, the metal is thoroughly cleaned to remove all dirt, rust, greases and oils. This allows good adhesion to the photosensitive resist to be obtained.

6. Resist Lamination
Photosensitive resists are UV light-sensitive polymers which are applied as a dry film to the metal either by hot roller lamination. The type of process used depends on the metal being used and the type of subsequent processing required. The coating is applied to both sides of the metal.
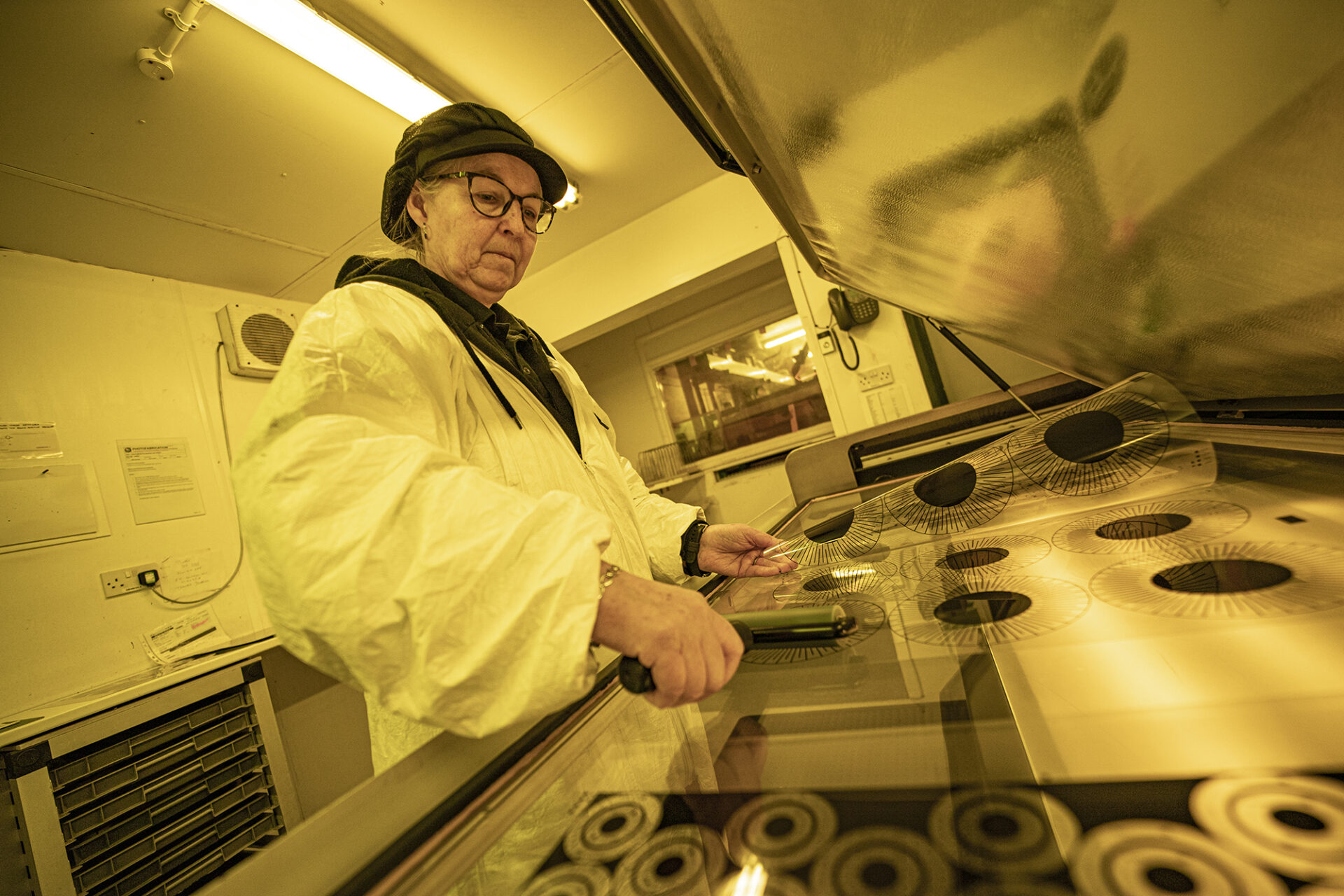
7. Printing
The Graphic Tool carrying the component image is now laid over both sides of the metal which has been previously coated with the photosensitive resist. The combination of Graphic Tool and coated metal is then exposed to UV light to transfer the image onto the metal coating.
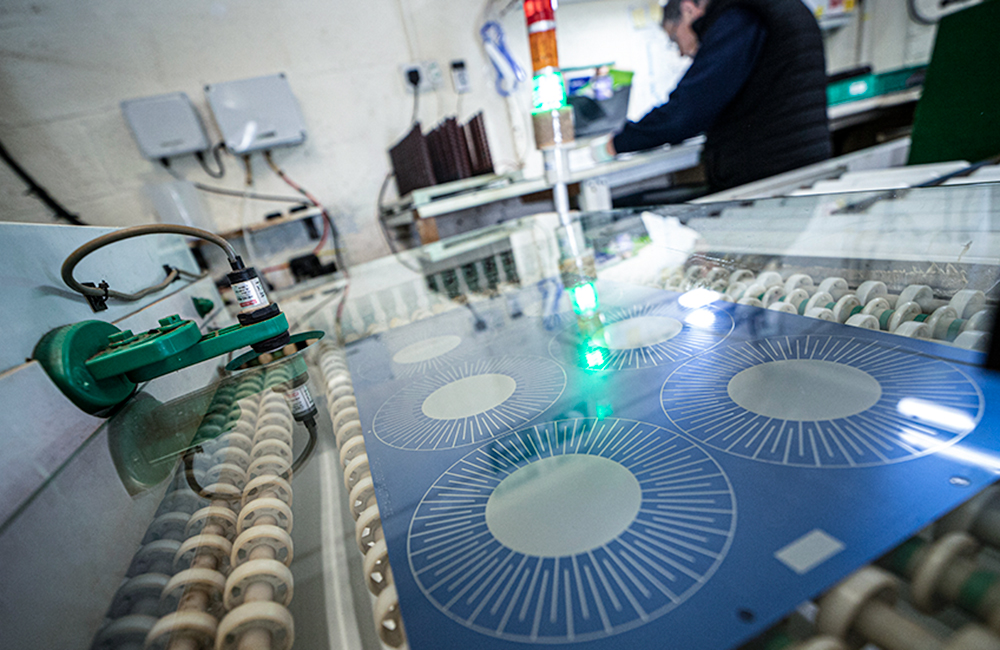
8. Developing
The area of photosensitive resist which has been protected from the UV light by the Graphic Tool, remains soft and is then chemically developed away leaving the metal exposed ready for etching. The component image remains protected by the resist.
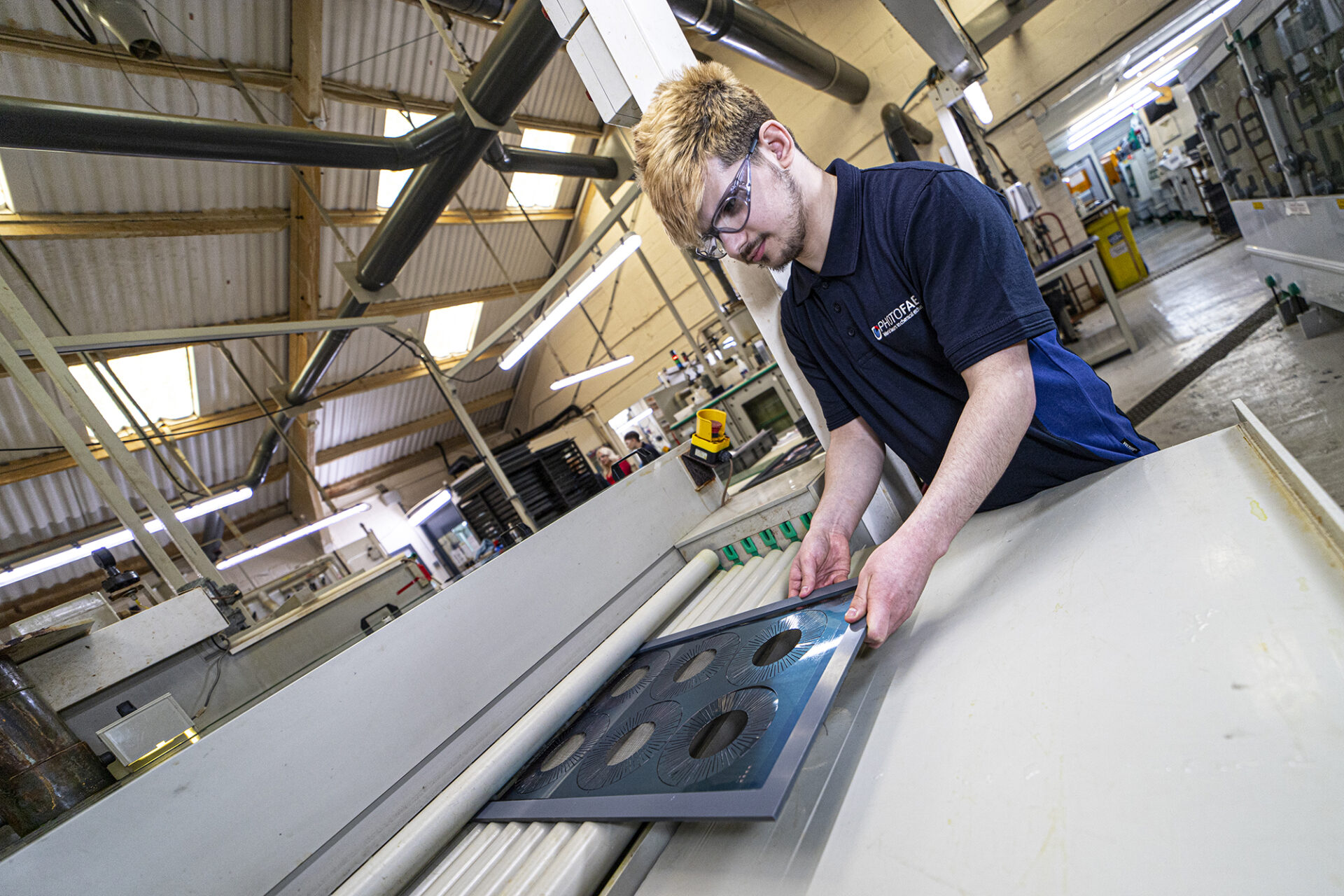
9. Etching
The prepared metal sheets are now passed through the etching machine to remove the exposed metal. Virtually all metals can be etched, although some are etched more readily than others. We have developed bespoke chemistry for a range of materials allowing us to offer the highest quality. The etchant is regenerated to maintain a constant etch rate and lower environmental impact.
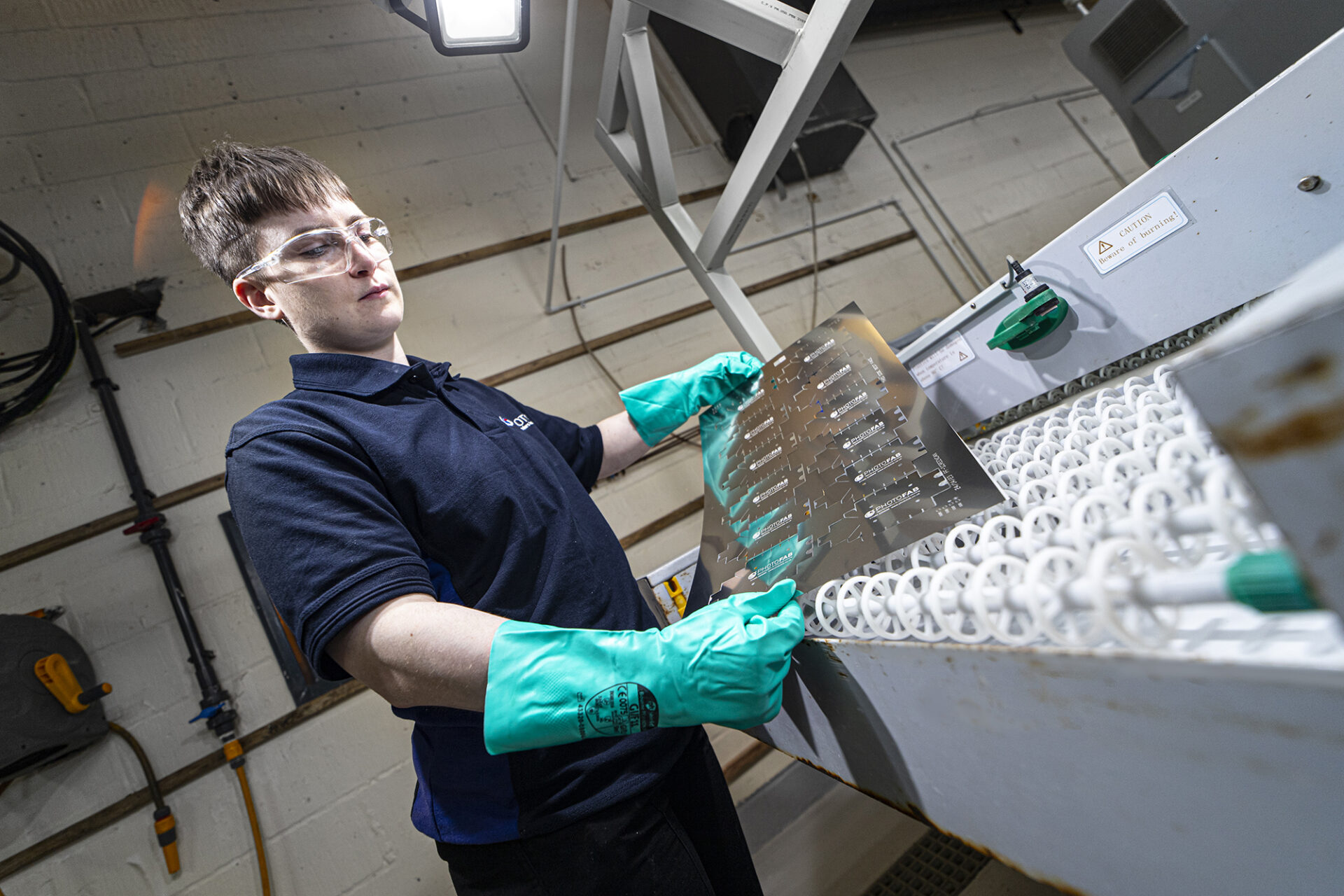
10. Stripping
The final process of PCM (Photo Chemical Milling) is to strip off the resist from the etched component and ensure that the metal is clean. A combination of automation and operator care is employed depending on the component specification.
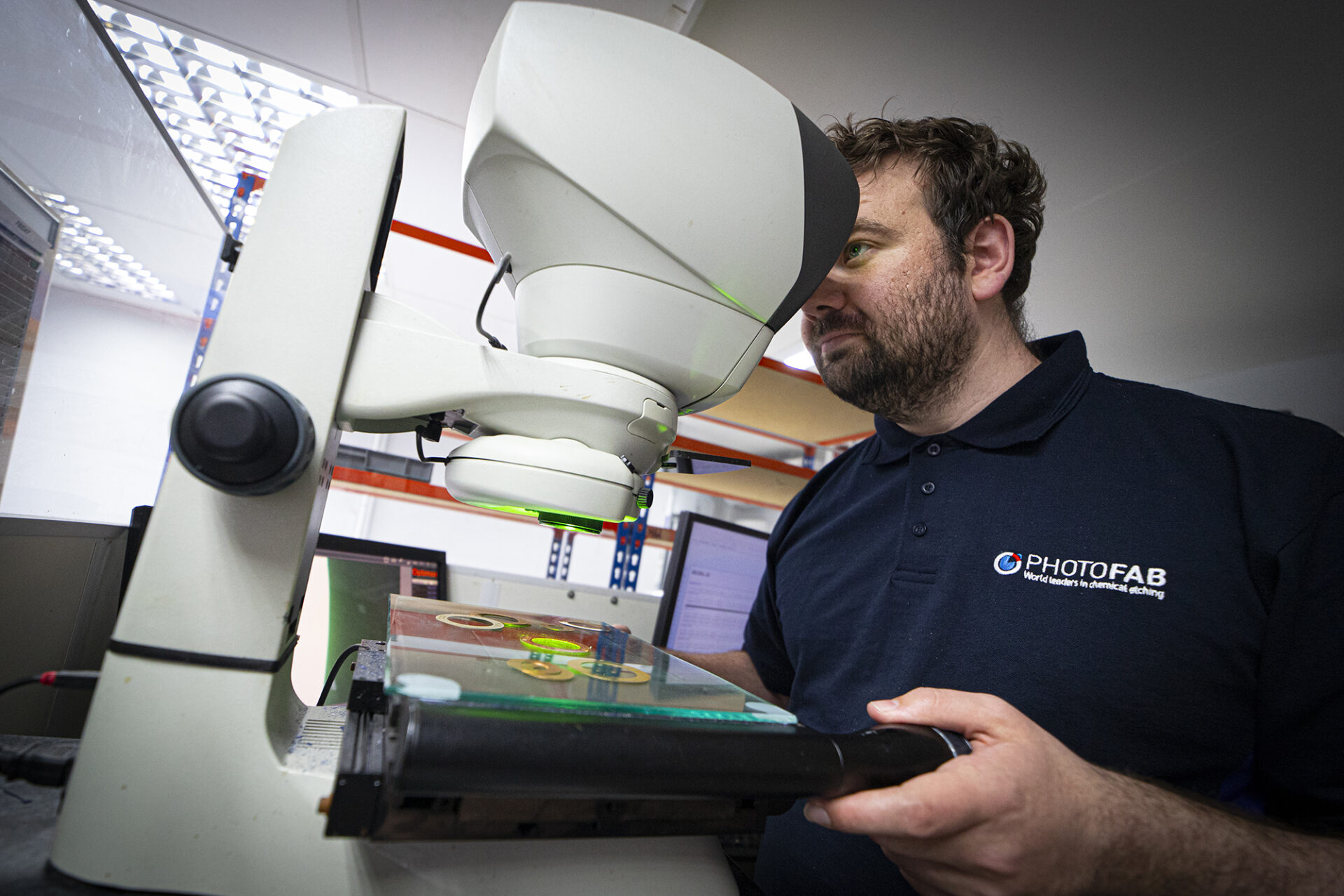
11. Inspection and Packing
The components are checked electronically to ensure they conform to dimensional specifications, and they are visually inspected for any surface defects. High quality finished products are then securely packed for overnight delivery.
Our etching tabbing GUIDELINES
In order to further increase the precision of components, we ‘tab’ parts into sheets of metal. Tabs are slivers of metal, that serve to retain parts in sheet form. In other words, once completely etched, the components are not ‘loose’ parts, but instead are held into sheet form using these tabs.
Photofab have devised four different tab styles. These are shown below along with features of each.
Inboard Twist Tabs
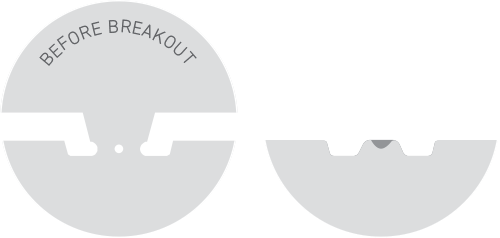
- Full thickness twist tab
- Leaves minimal material loss and no protrusion
Half etch outboard tabs
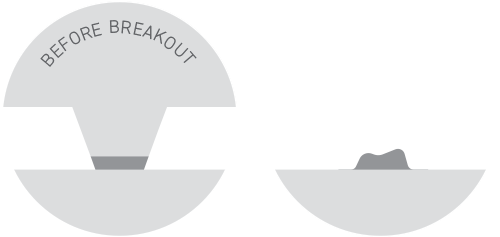
- Used when small protruding witness is acceptable, or when inboard is not an option
- Can be finished on thicker materials to remove protruding witness
Half etch inboard tabs
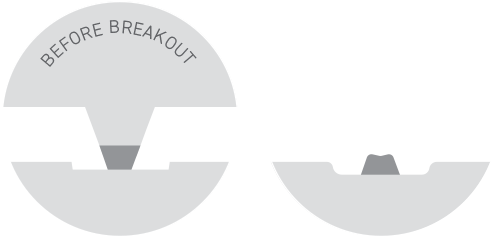
- Half etched break line style
- Used when a small protruding witness is not acceptable
- Breaks slightly inboard or on the component edge leaving no protrusion
Full thickness outboard tabs

- Used when small protruding witness is acceptable – or when inboard is not an option
- Can be finished on thicker materials to remove protruding witness
*1mm is not the dimension of the feature, but is for scale reference only
Tab-less parts can be made if required.
Etching Tolerances
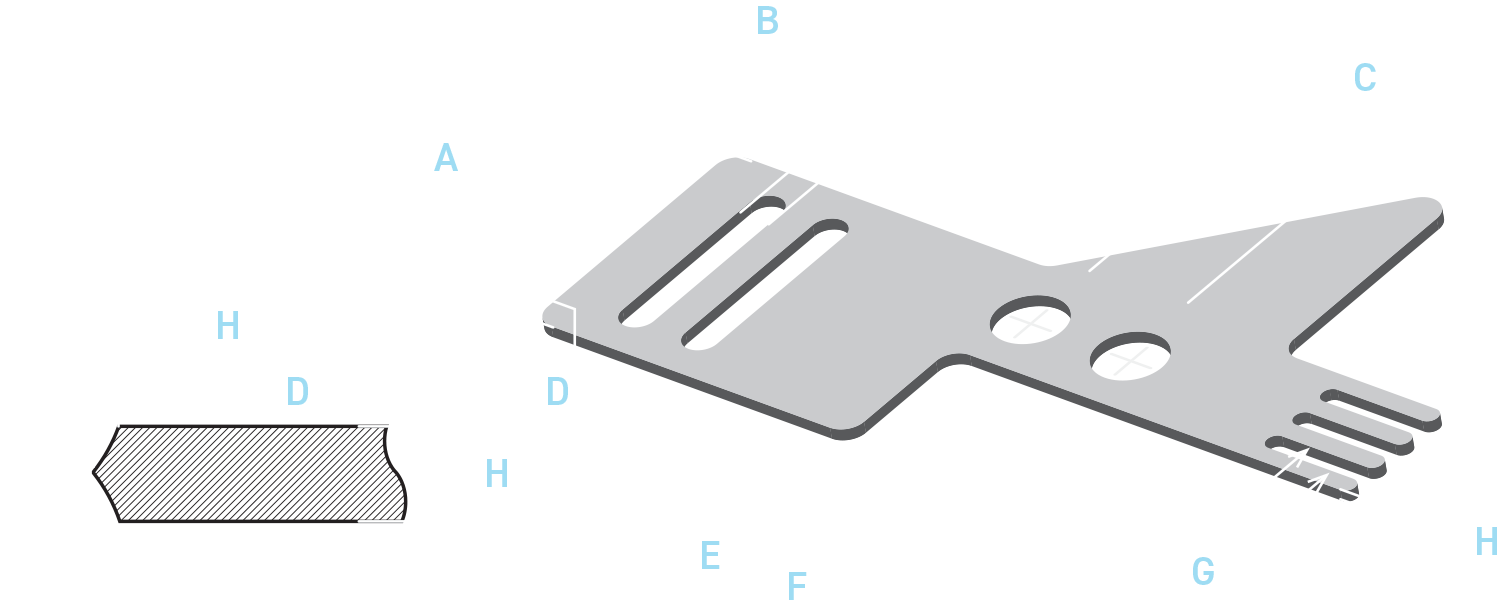
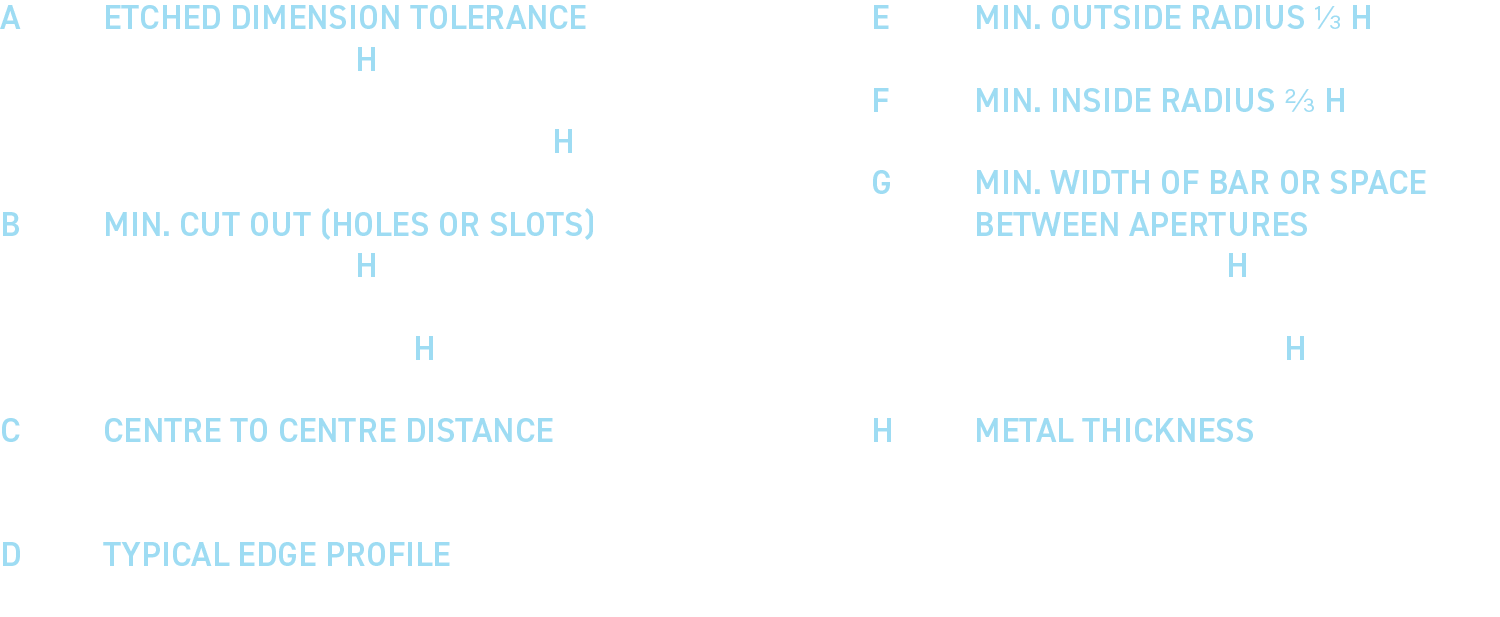
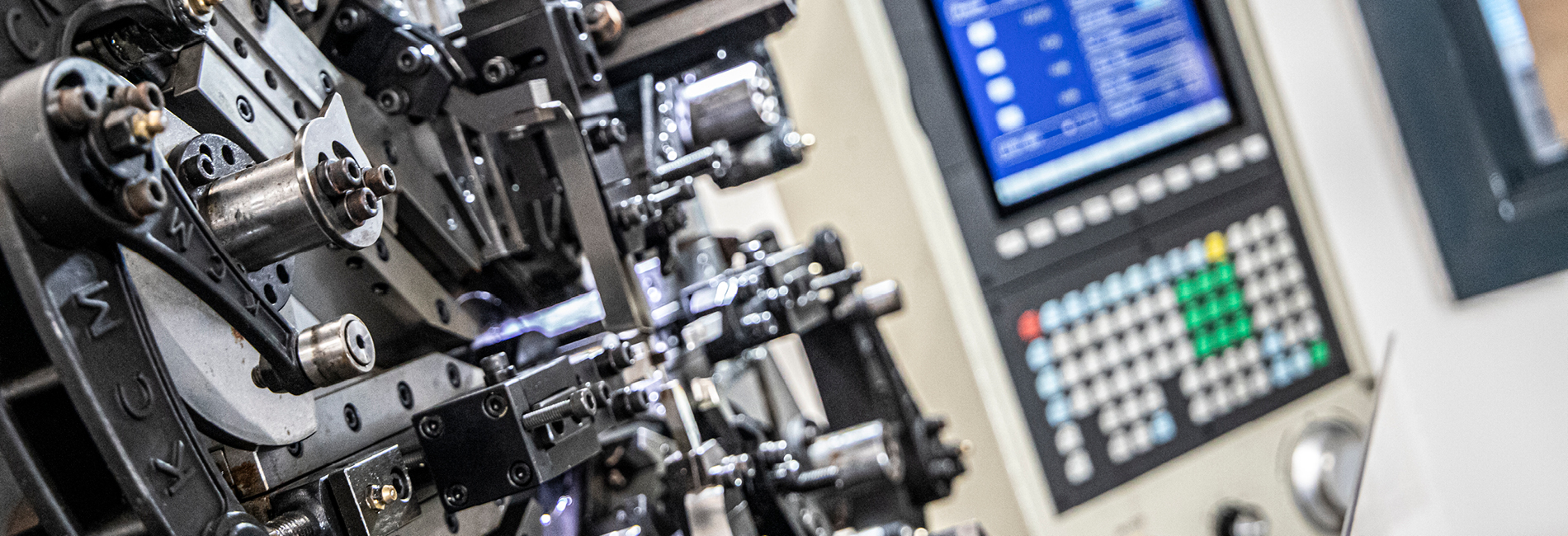
Dedicated engineering
To support our world leading etching division, we can now offer toolroom, forming and finishing as part of our full-service offer or as a stand-alone service. Customers can now enjoy the flexibility of enjoying the convenience of full-service manufacture or pick and choose services to suit them.
Along with 100’s of stock universal tooling and capabilities for custom tooling, including custom multi-slide tooling for specialist radial forming. This is backed up by a highly trained team and a multitude of presses. Photofab have also invested in a new high impact press for forming thicker metals.
Why work with us?
We also put great emphasis on customer service, where our dedicated account managers are your expert single point of contact. Supporting you with anything from technical and design questions through to quotes, orders, delivery and everything in between. We strive to offer the best customer service experience in the industry. We take immense pride in being able to push the boundaries of chemical etching with our commitment to continuous improvement. We are constantly refining our processes to deliver the best possible results and service to our clients. If you are looking for intricate metal components, why not try chemical etching? We would love to work with you.
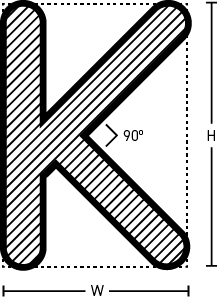
KNOWLEDGE
Over 55 years of expertise and experience with a highly trained team of specialists delivering high volume orders.
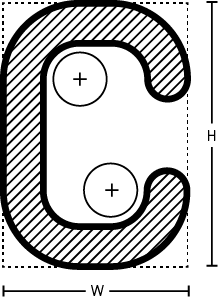
CAPACITY & SPEED
For cost-effective full volume orders of hundreds of thousands. We also offer fast turn-around, as little as 24 hours.
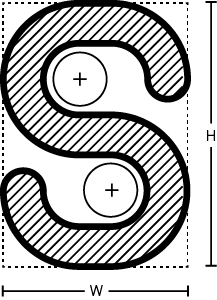
SERVICE
Our dedicated account managers are experts and there to help, advise and manage.
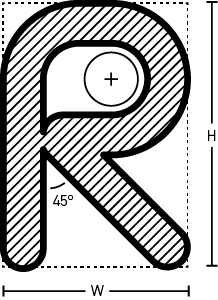
RELIABILITY Trusted by thousands of OEMs to deliver quickly and accurately.
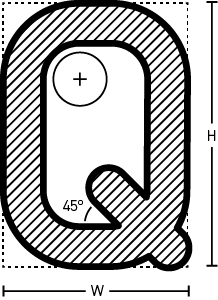
QUALITY SC21, ISO 9001, 14001 & 45001 quality processes.
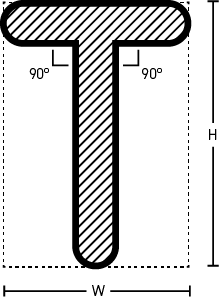
TRACEABILITY Fully traceable materials and processes.
Add us to your supply chain
From short run formed prototyping to high volumes with a 98% On Time Delivery track record, we aim to exceed your expectations. Call our account team today on 01480 226699 or contact us now to see how we can add an extra dimension to your manufacturing project. Keep up to date by following us on LinkedIn.
To find out how we can help you