Photofab’s etching experience is just what Vision Engineering needs
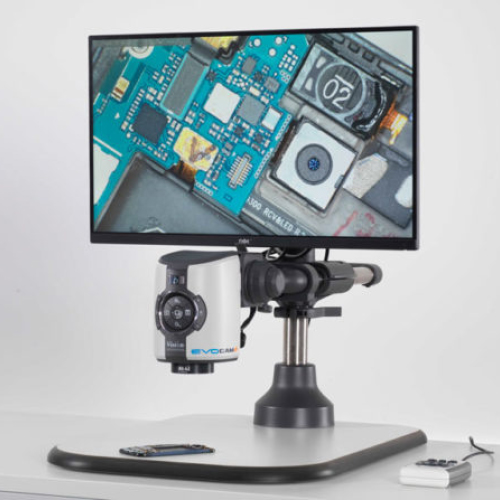
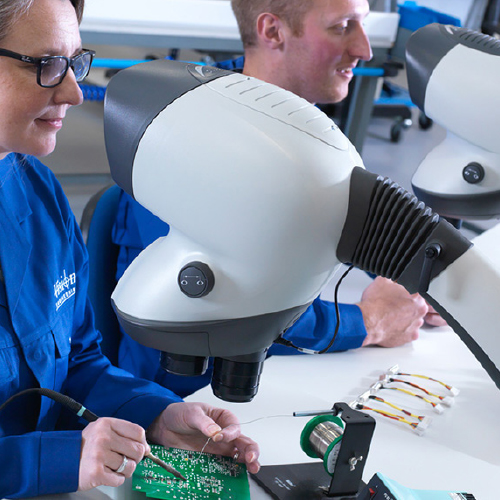
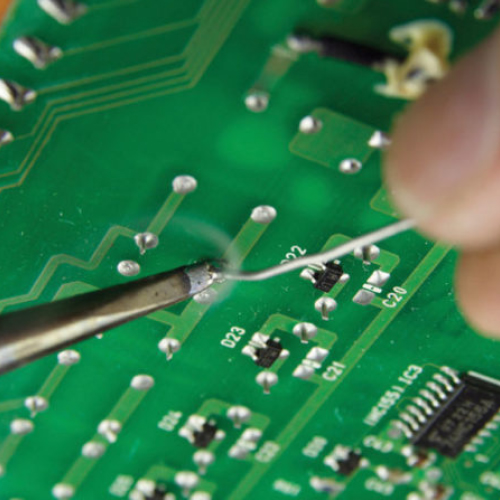
About Vision Engineering
Vision Engineering was created in 1958 by Rob Freeman, a toolmaker with the Jaguar racing team in a shed the company’s global headquarters proudly sits next to the site where it all began. Rob’s drive and appetite to create innovative products put the company on its road to success and Vision Engineering holds many world patents for optical technology.
One of their products, Mantis, is the world’s first eyepiece-less stereo microscope, and was launched almost 30 years ago. Mantis has evolved significantly since its original design and Vision Engineering is currently manufacturing the fourth generation Mantis. The product is used across the world in electronics, medical devices, packaging, automotive, and aerospace industries and for any application requiring inspection and rework.
In 1994, Mantis manufacturing moved to Connecticut, USA, where it is still manufactured today. Alongside its headquarters in Woking, and offices in Connecticut, the company also has offices in Europe and Asia.
The brief
The company attributes its success to innovation and development of new technology to improve quality in manufacturing, by inspection and measurement.
In order to maintain this, Vision Engineering needs precise components made to exact accurate measurements from a company that can turn an idea into a product quickly and without fuss. This is where Photofab comes into the process, providing accurate parts without the significant waiting period.
“Significant R&D investment in optical and digital technology continues with recent patented technological breakthroughs heralding the next step in innovation and market penetration for Vision Engineering.”
Mark Curtis
Managing Director, Vision Engineering

Solution
Vision Engineering likes to use Photofab because their idea, even in a basic hand-scribbled format, will be created exactly how they need it with minimum fuss and a very swift turnaround. Because Photofab has employees with a basic understanding of what the customer is doing with the parts, or what they are trying to achieve, advice can be offered, and potential alternatives to any issues on a case-by-case basis.
Due to the nature of the Vision Engineering processes, they require very accurate measurements, which is only possible using Photofab’s process of etching. Photofab has a long trading history with Vision Engineering and a great working relationship where both companies understand exactly what the other needs to make things work.
The result
Vision Engineering has, at times, needed a quick turnaround, which Photofab has satisfied within three days of the order being made. Etching was found to be the better solution for Vision Engineering’s requirements when compared to laser cutting, which often leaves burrs that need further processing. Photofab can now offer Vision Engineering a tighter overall tolerance and a better lead time than laser cutting, where two to four weeks is considered to be standard waiting time.
“We are proud to be associated with world market leaders like Vision Engineering. They appreciate we have an excellent workforce, a wealth of knowledge and experience gained over more than 50 years that allows us to come up with the solutions Vision Engineering needs. Our relationship is forged on trust – long may it continue.”
Brett Robinson
Sales Account Manager, Photofab
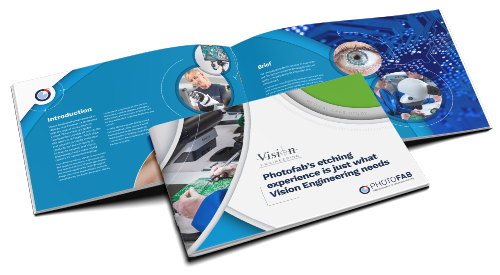