Photofab delivered when it mattered most for the medical sector, with our supply pivoting heavily towards ventilator components during the recent COVID-19 pandemic. Chemical etching offers a cost-effective way to mass produce small, intricate components for use in devices such as ventilators, but also in many other medical devices.
This essential equipment relies on a range of components that can be produced with chemical etching. Our capacity allowed us to support the medical sector during the pandemic and into the future.
For more information on how we can reduce your costs & improve lead time contact our dedicated account managers on 01480 226699 or email enquiries@photofab.co.uk.
Download our brochure to learn more about Photofab and the medical sector:
Support when it was needed most
The Covid pandemic created an environment where the rapid manufacture of essential medical equipment became the number one priority for the companies supplying the NHS. Photofab were proud to assist by producing with priority a range of components essential to ventilator equipment.
We are fully set up to provide precise and rapid manufacturing for components in medical devices. Using our highly experienced team we are already working alongside a number of key supply networks, having increased our capacity to allow for further support.
Fully Accredited for medical
We hold various ISOs and are SC21 accredited and manufacture fully traceable, high-quality components with full process control capabilities and complete confidentiality. Our trusted logistics partners enable us to deliver on time, every time. Photofab also offer the highest levels of customer service, with a dedicated Account Manager to help, support and manage your project throughout the entire process.
We have produced the following components for the medical sector:
- Muscle clamps
- Surgical/bone saws
- Microscopes
- Mesh
- Shims for virus testing kits
- Clips for medical masks
- X-ray receptor plates
- Valves for inhalers
- Ventilators
- Respirators
- Shims for ventilators
- Filters
Photofab are able to offer such a wide range of products due to the ongoing and investment we put into our processes to ensure we have the latest technology in the industry. This, combined with the vast technical experience our staff have in the chemical etching industry show that we really are your complete supplier. Photofab have worked with some of the finest minds in medical sector development to bring specific products to both the marketplace and the surgeons who need the best possible equipment.
DEDICATED engineering
Photofab understands the importance of skilled engineering when designing components and putting them into production. Therefore, we have heavily invested in a dedicated secondary engineering unit, the aim of this is to offer an even greater service and flexibility to our customers.
Originally set up to provide an in-house solution to support the etching division, it has proven so popular with our customers that Photofab are now offering toolroom, forming and finishing as stand-alone services. This means our customers now have access to a new level of flexibility – enjoying the convenience of full-service manufacture or pick and choose services to suit them. It truly is a complete service from Photofab.
Photofab continues to offer cutting-edge services and outstanding lead times, and we can do so because of continuous investment in our people and our processes, leading to class-leading output and lead times – including our rapid 24 hour turnaround service.
The benefits of
working with us
We are world leaders in the development of photochemical technology to produce intricately shaped components. We have produced over 80,000 different components over the years and are highly regarded for our chemical etching process. Our engineers offer many services that you can find here, and will offer advice to improve the product and reduce the costs.
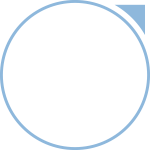
24-hour quotation service
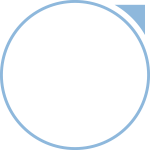
Dedicated account managers
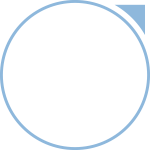
Rapid manufacturing service
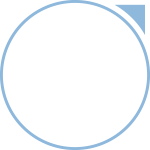
Cost saving stock of uni-tooling
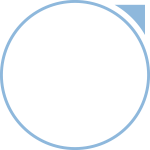
Etched fold lines for tool-free forming
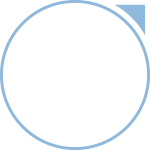
Full manufacturing service and supply chain management
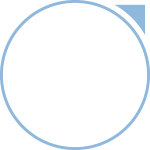
Access to manufacturing and technical advice and expertise
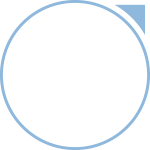
Quality accredited to ISO 9001, ISO 14001, ISO 45001 and SC21 Bronze
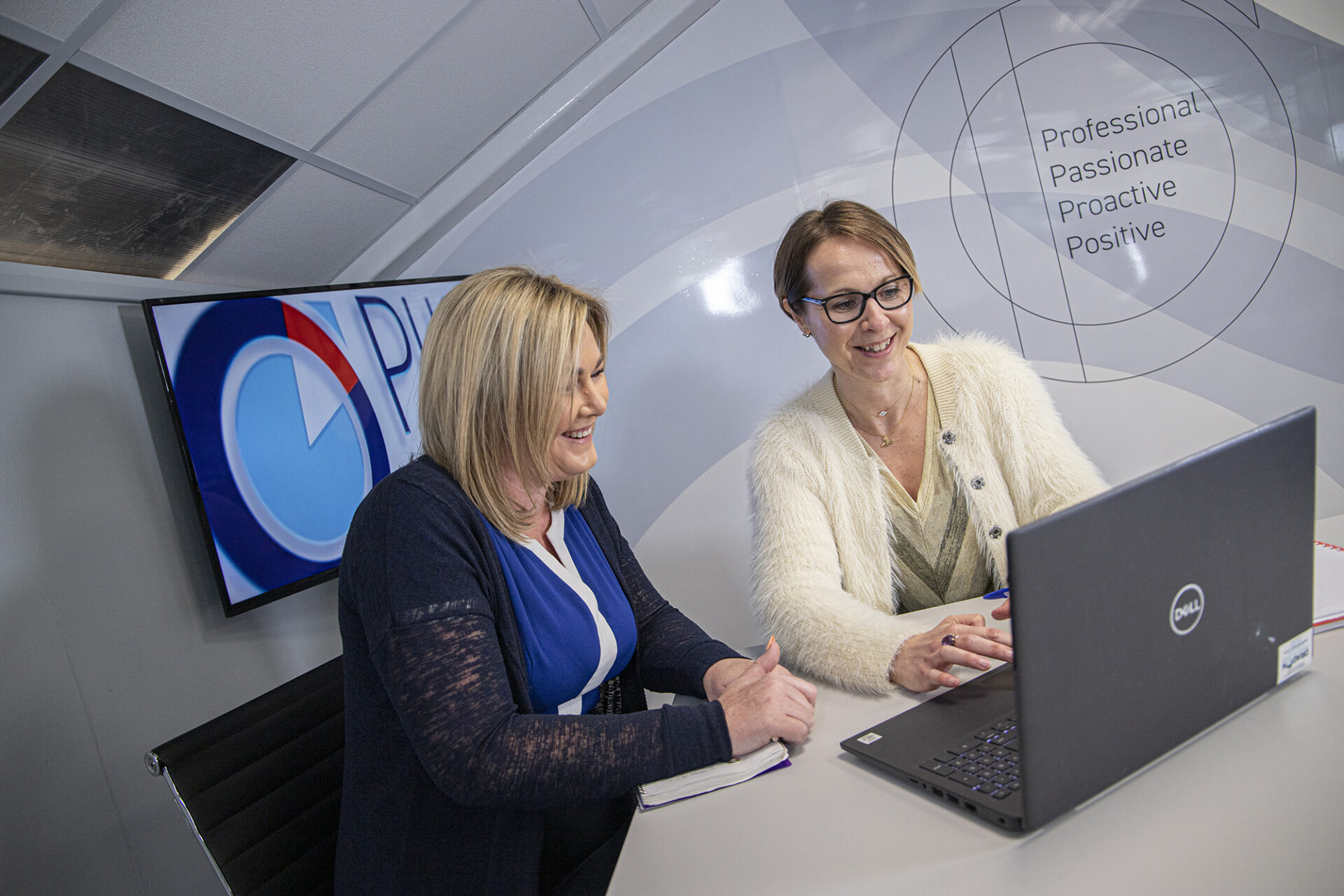
The Photofab difference
One of the key reasons Photofab enjoy its customer retention and longevity is the team of dedicated account managers. This ‘single point of contact’ throughout the whole process, ensures a personal service, and pride in the quality and reliability of the entire Photofab service.
Customers rely on their dedicated contacts’ understanding and in-depth knowledge of their specific requirements and know the highest standards will always be met using the most efficient and cost-effective methods.
This consistent customer service is the foundation of our customer loyalty and is maintained throughout every department and every stage of production. Put us to the test for your next project and call one of our account managers on 01480 226699 or use our customer enquiry form, we would love to hear from you.
start your production journey today
If you are looking to find a complete service include dedicated engineering to design and implement your solution, get in touch with us. You’ll be given an account manager who is always on hand to advise and take care of everything for you. Call Photofab on 01480 226699 or contact us now to see how Photofab can add an extra dimension to your manufacturing project. Keep up to date by following us on LinkedIn and Twitter.
TAKE A LOOK AT OTHER
SECTORS PHOTOFAB Supplies
To find out how we can help you
Get in touch today
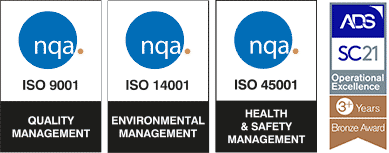