Accelerating development of scientific and optical equipment hinges on component accuracy
The scientific and optical industries share common goals and demands for the components proving critical to equipment performance. Photofab’s core capability set has been meeting quality, reliability, and accuracy demands for decades but an accelerated drive for more innovation and mass market adoption has generated a time to market challenge that puts more pressure on the supply chain.
This blog looks closely at how Photofab not only serves the industries today, but how it will ensure its position in the future as technological advances break through.
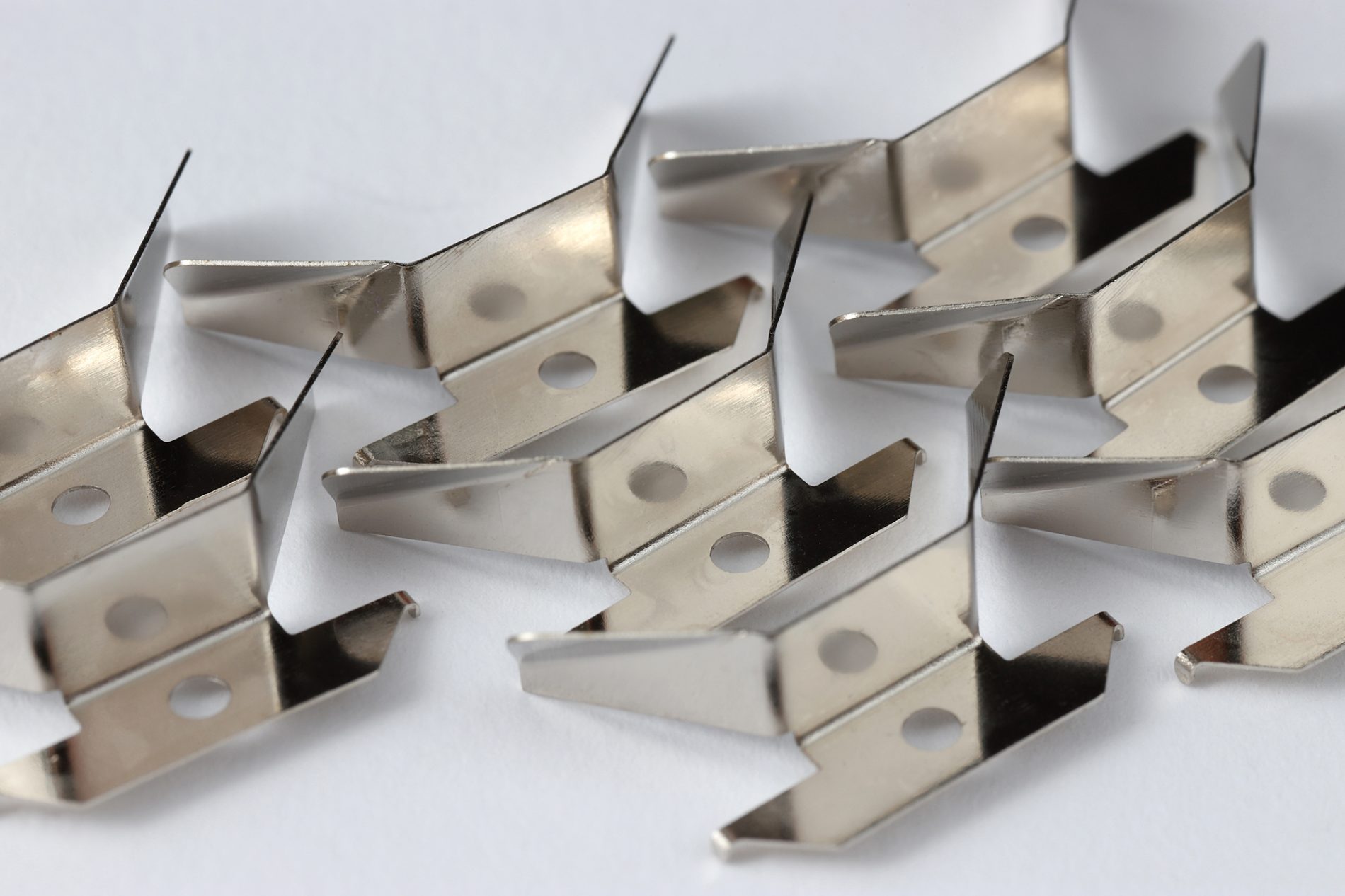
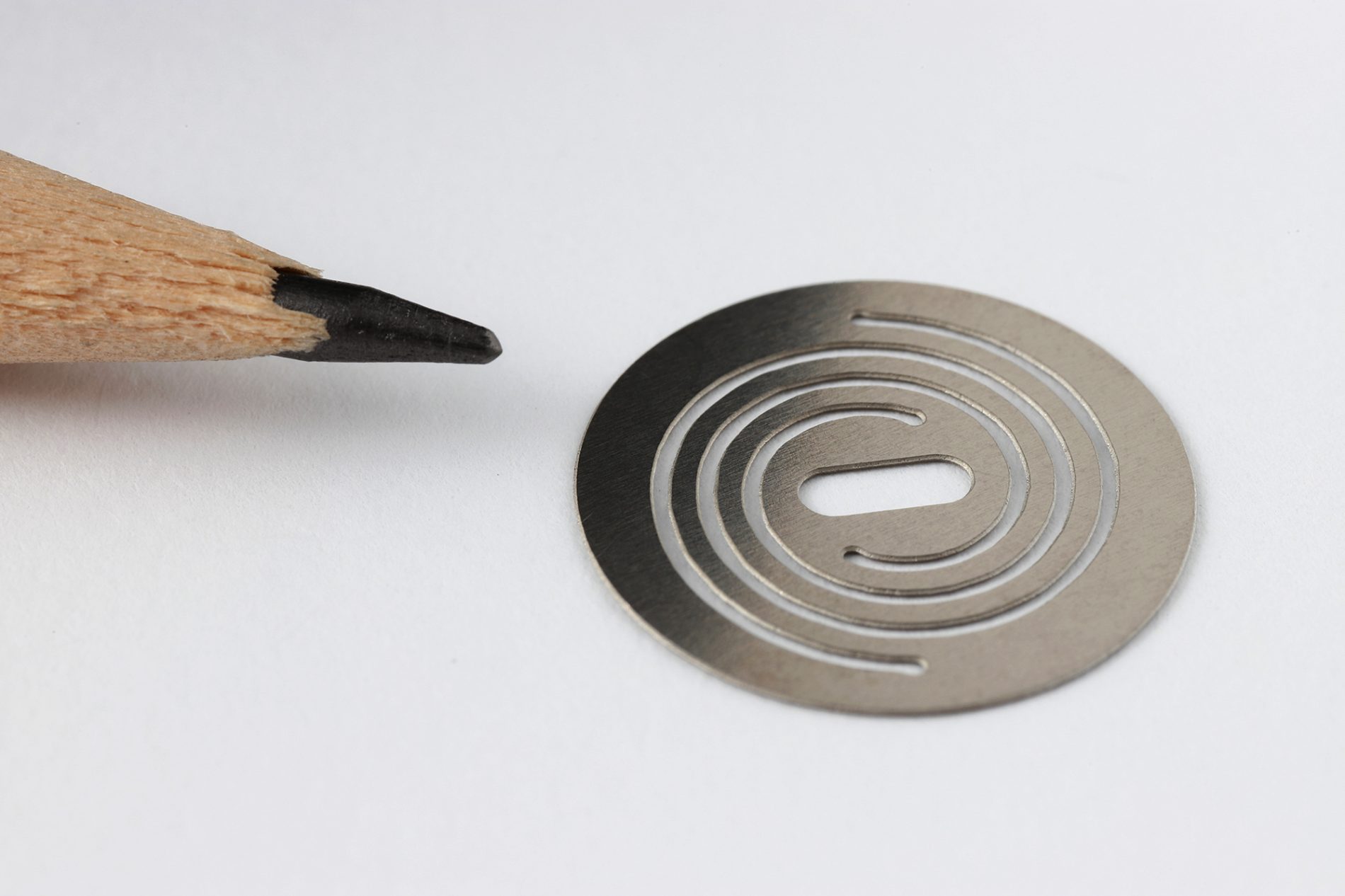
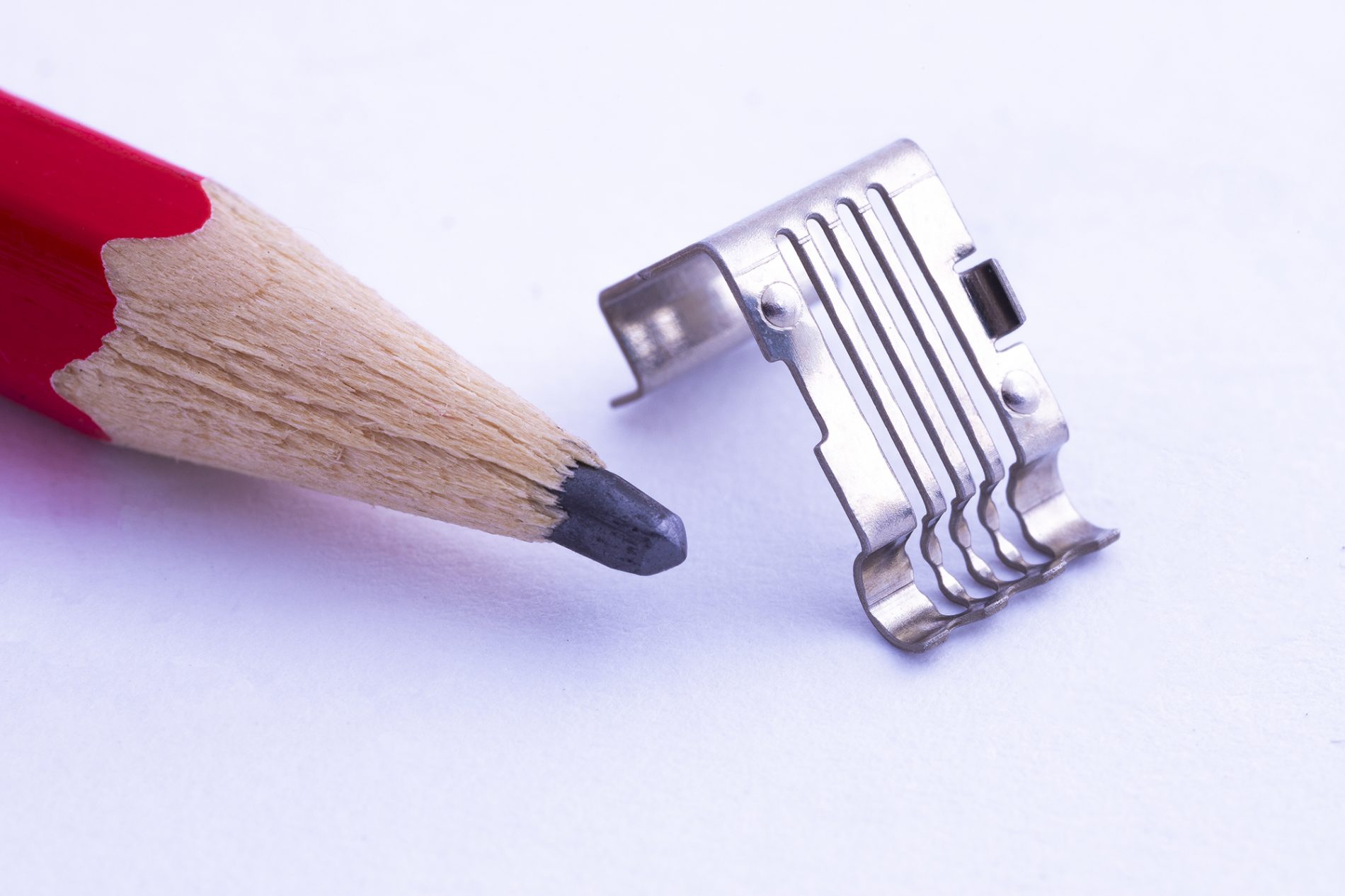
Small parts and big discoveries
Scientific instrumentation must be incredibly accurate and evolve at pace to work alongside a developing world. The tools and apparatus used to gather and evaluate scientific research are becoming more and more accurate. And for accurate readings, the small components that have become so critical to such devices working effectively have to mirror this accuracy with micron tolerances.
For those small parts, the technique of chemical etching is a distinguished method to satisfy the stringent demands on quality and tight tolerances. Furthermore, the ability to prototype at speed and adjust designs with more flexibility than alternate metalworking methods makes it particularly well-suited to sectors placing R&D and innovation high on the agenda.
It’s nothing new though. The need for precision components in scientific apparatus has been a requirement since Photofab’s inception some 50+ years ago. Yes, the quality demands increase and metalworking suppliers with flexible manufacturing processes are ideal partners, but there’s a new emphasis on how the industry itself is developing.
More than any other time before, a worldwide pandemic put the work of scientists firmly in the public spotlight. It has turned the last year into a pivotal one for research and development, scientific innovation, and technological progress. Covid accelerated the ways in which the industry operates and there is more collaboration and a reassessment of processes that has resulted in increased speed to market.
The speed to market challenge is a big one and relies on manufacturers with efficient processes and clear supply chain visibility. To decrease foreign dependencies, there is a growing trend to reshore, and manufacturers of scientific equipment were some of the first to bring the supply of critical components closer to home. Many others will need to outsource where they once manufactured themselves, as demand will outpace their capacity and the lack of enough skilled people, space, and advanced manufacturing processes will become barriers.
Photofab has become a critical partner to many organisations that are benefiting from outsourcing manufacture of components and investing the time saved into R&D and progressing new innovations. Whilst accelerated by Covid, it’s a methodology that will very likely stick in this industry as the spotlight shows no signs of dimming.
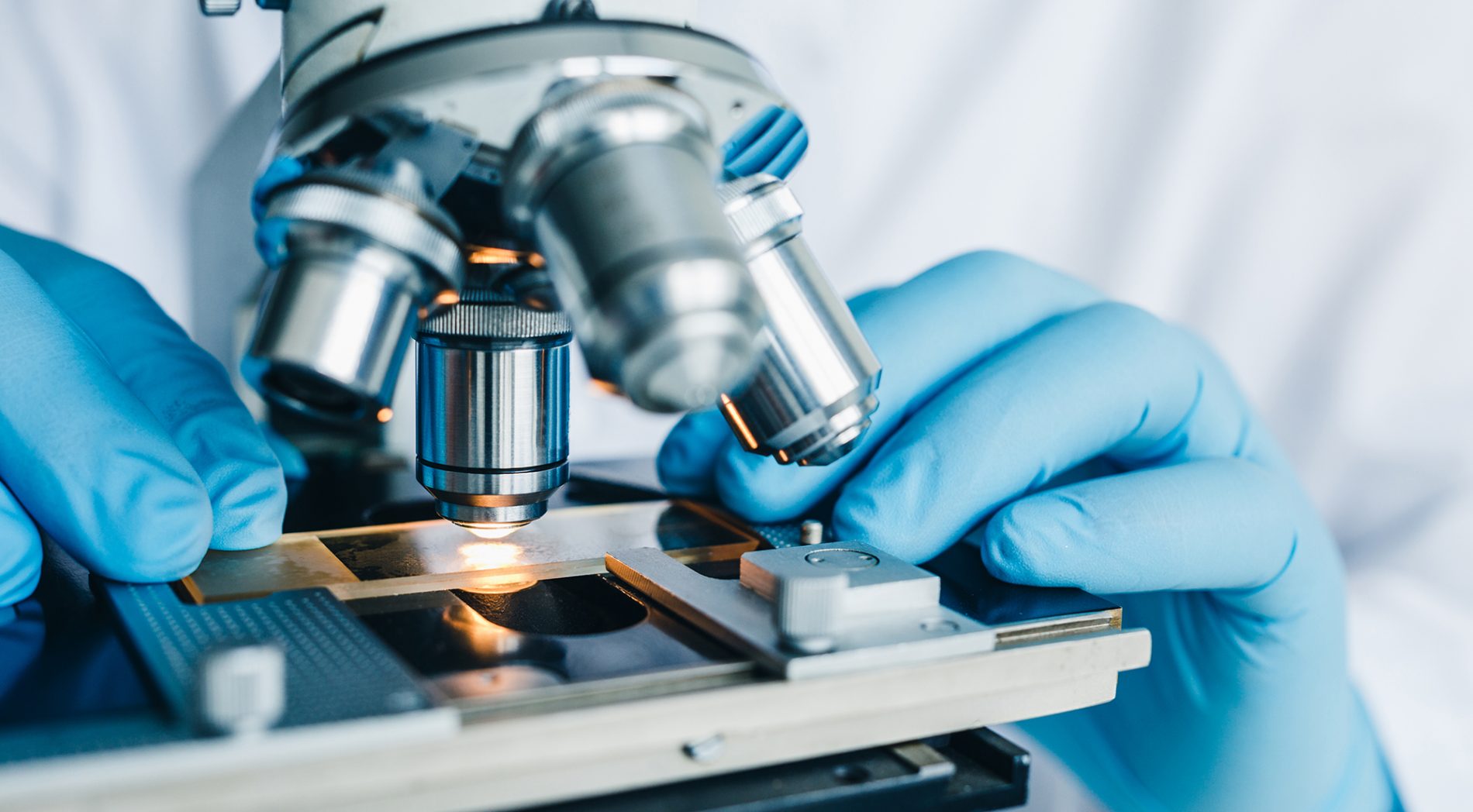
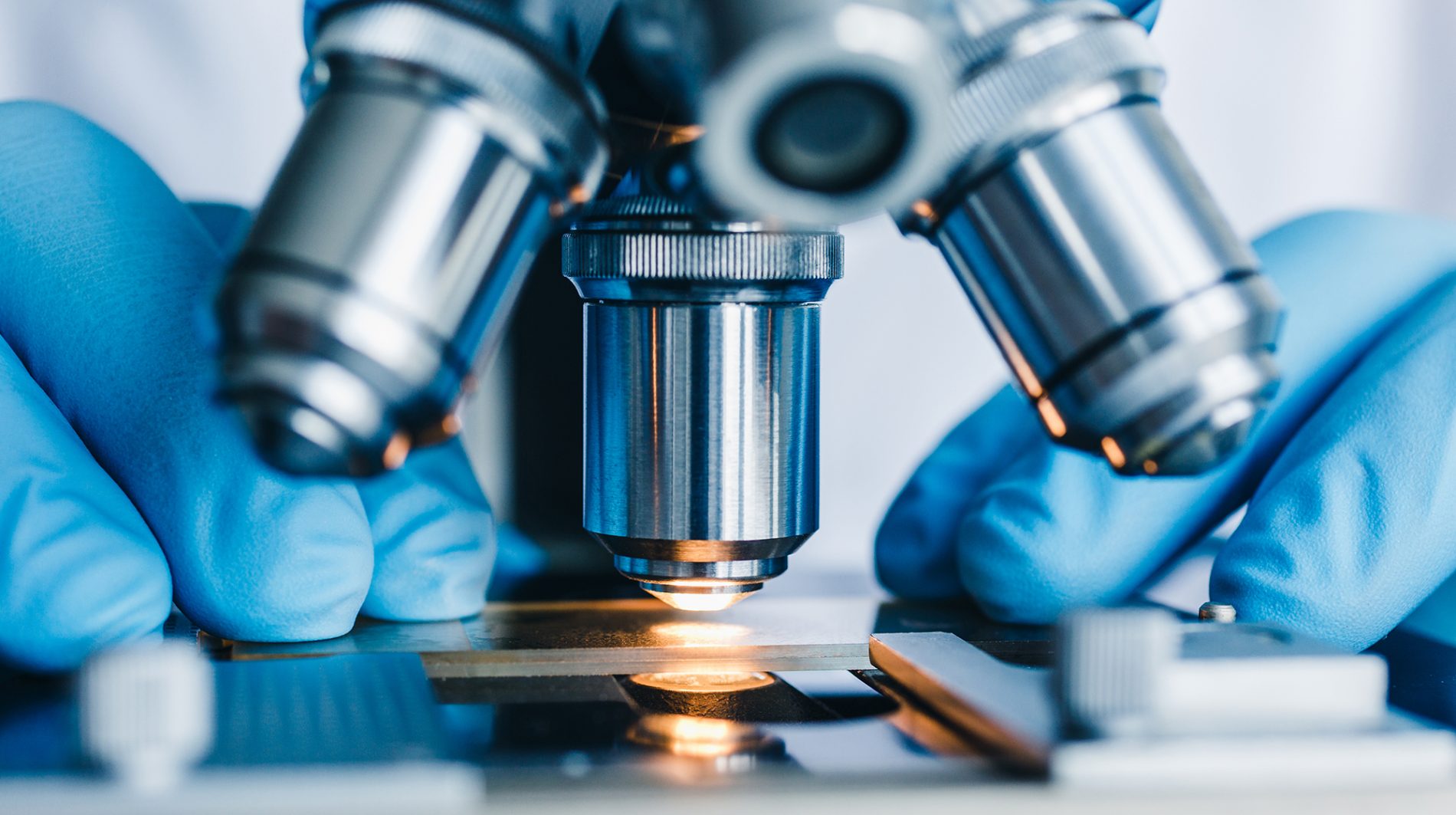
A view of the optical sector
The optical industry encompasses much more than simply just “eye care”. The sector is focused on helping people with their vision, but it goes further than the glasses and contact lenses that are commonly associated.
For people to improve their vision, there are many different tools and machines that need to operate effectively. Usually before being given glasses or contact lenses, people have eye tests, where they are put through a series of vision exercises involving cameras and screens, or even laser eye surgery; these all require small, precise, and reliable components.
The demand for high levels of quality, traceability, and fast lead times on stress and burr free components shares commonality with the scientific industry. Photofab has invested in the people, technology, and manufacturing processes to provide this capability and has formed a close bond with manufacturers of optical equipment over the years.
Beyond these typical demands, there are services that Photofab has fine-tuned to provide the optical industry with sought-after added value. PX-3 chemical black coating for example gives components a non-reflective overlay to prevent corrosion and reduce light reflection. This is just one of many examples where quality control measures are ensuring customer satisfaction.
With these capabilities and added value services embedded into the very fabric of the business, Photofab is prepared for the technological advancements of the optical industry and the demands it will have for component manufacture in the near future.
And that future is an exciting one. Advances in Augmented Reality (AR) displays is a worthwhile example to explore. These technological advances are encouraging the optical industry to drive mass market adoption of AR wearables, such as smart glasses. They enable users to see digital images overlaid on top of the real world.
Performance of these wearables will be reliant on the associated projectors which are proving critical to the overall AR system. And no prizes for guessing that these projectors contain small chemically etched components with tight tolerances. These components are helping to maintain key parameters such as luminance, colour uniformity, and contrast. Photofab works closely with R&D departments at several manufacturers of wearables and other devices adopting AR technology. The close partnership is critical to ensuring new design requirements can be prototyped at speed and there is no disruption on the path to mass production.
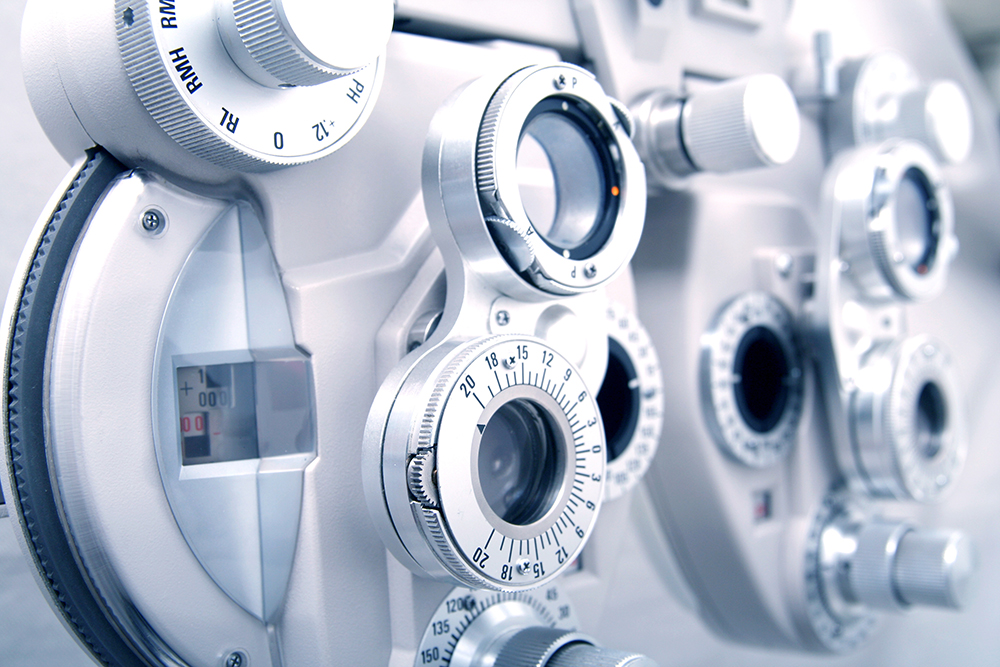
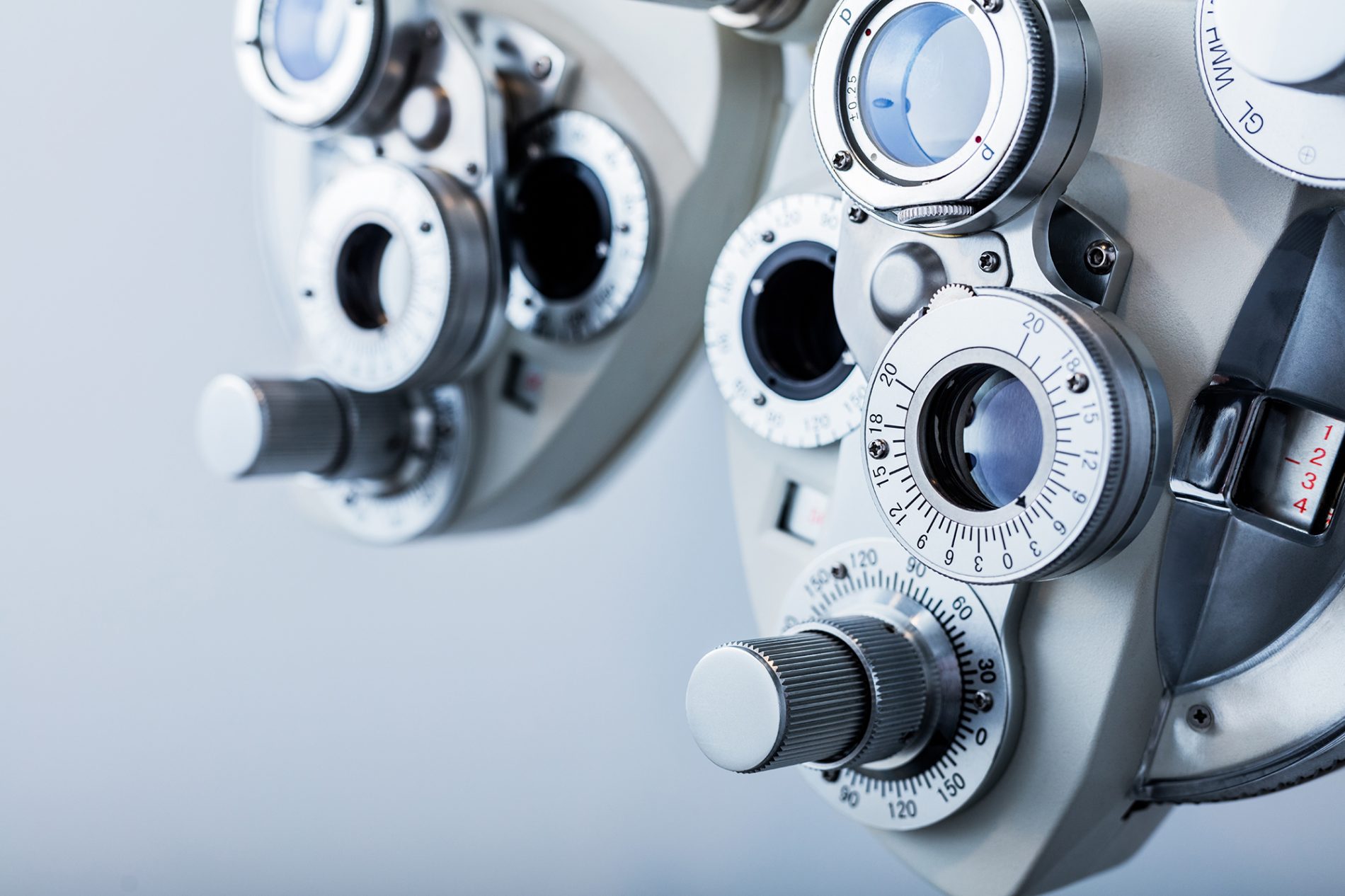
Summarising the sector commonalities
Whether it is scientific apparatus or optical wearables, both industries share commonality for precise chemically etched components and partners who can manufacture to both tight tolerances and tight lead times. Fast component prototyping capabilities are offering R&D departments in both sectors more time to innovate, test, and refine their products. Continuous investment in people, technology, and processes at Photofab has cemented its position as a reliable supplier to both industries and it is these investments that will ensure its position for years to come.
To engage with Photofab on your next project and benefit from reduced lead times and costs, a rapid prototyping service and decades of industry know-how, use the contact page to tell Photofab what you need and see just how quickly the team respond!
For more stories like this, follow Photofab on LinkedIn and Twitter.