Driving the automotive industry
Since the dawn of the motor vehicle, the automotive industry has come on an unfathomable journey. The need to innovate has changed the way we think about road travel, and particularly the demand for renewable energy and electric power has skyrocketed as consumers look to lessen their impact on the environment.
As the automotive industry has been, and always will be, changing and developing to best meet the complex needs and wants of consumers, Photofab’s manufacturing must adapt to meet the needs of the sector.
Vehicles are featuring more and more technological advancements as the days go by, and manufacturers who work on every part of these vehicles will need to remain aware of these changes in order to compete.
Moving up a gear
We may not yet have got to the stage of flying cars as predicted in Back to the Future II, but technology in our vehicles is still making huge strides. Increasing sales of electrified vehicles could dramatically reshape the fortunes of the automotive and utilities sectors and propel the rise of a multibillion-dollar battery industry, and Photofab’s role in the sector is helping vehicle owners to reduce their emissions.
Photofab’s components are used in several products, including fuel cell plates for zero emission vehicles, which we will touch on later. The company’s components are also used for shims and spacers in Formula One engines, tread plates and speaker grilles on premium vehicles, and damping shims for fuel injection.
To achieve the precise requirements needed for these components, chemical milling is the ideal manufacturing method. The technique allows for the highly accurate production of parts, which is extremely necessary for an industry that relies on intricate detail across the board; accuracy can go down to as little as +/-0.025mm with Photofab, along with a broad selection of materials and finishes. Photofab’s chemical milling services keeps costs low, and its experience of using it across several projects and industries gives customers the confidence that they are in capable hands, ready to tackle whatever challenge the sector has next.
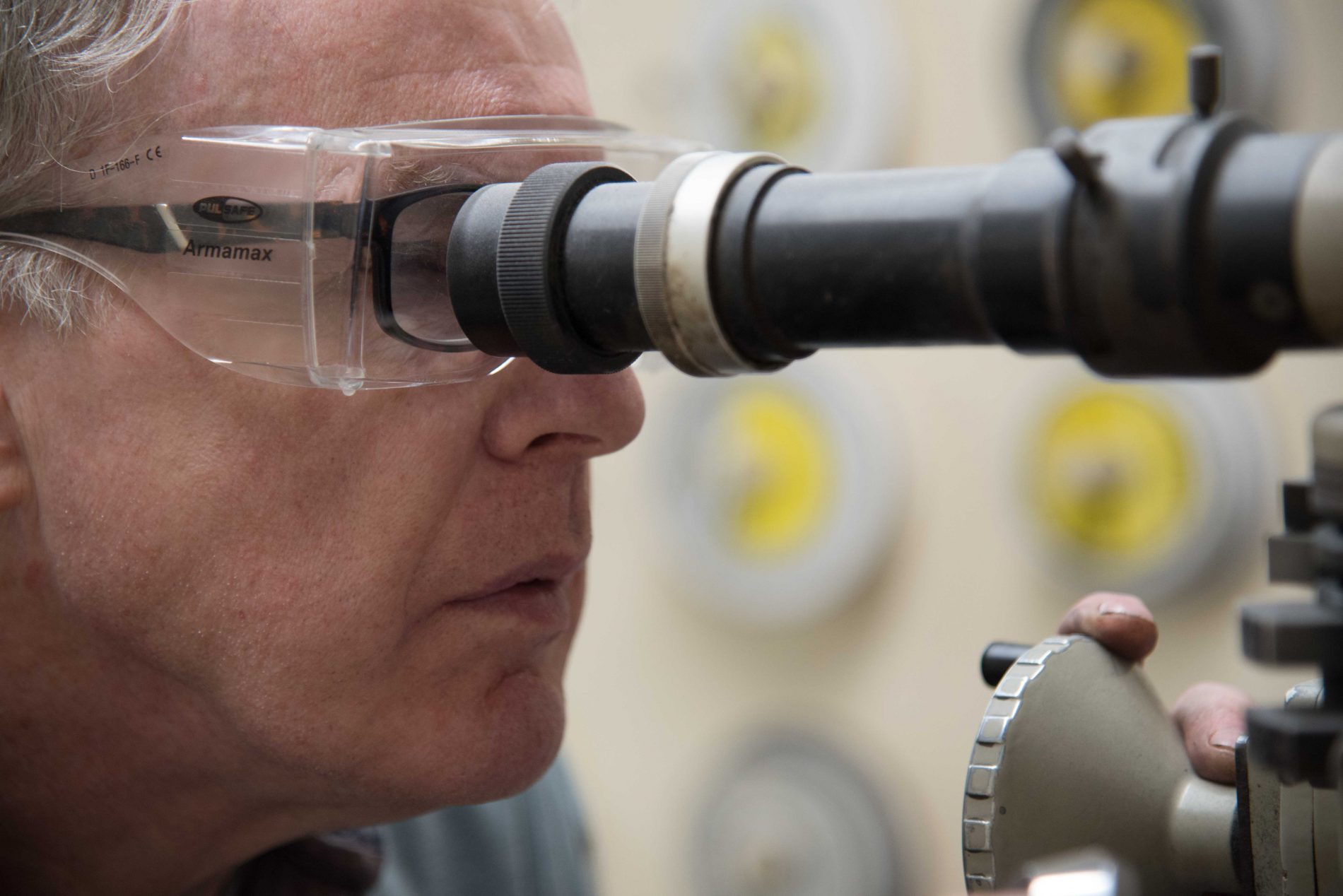
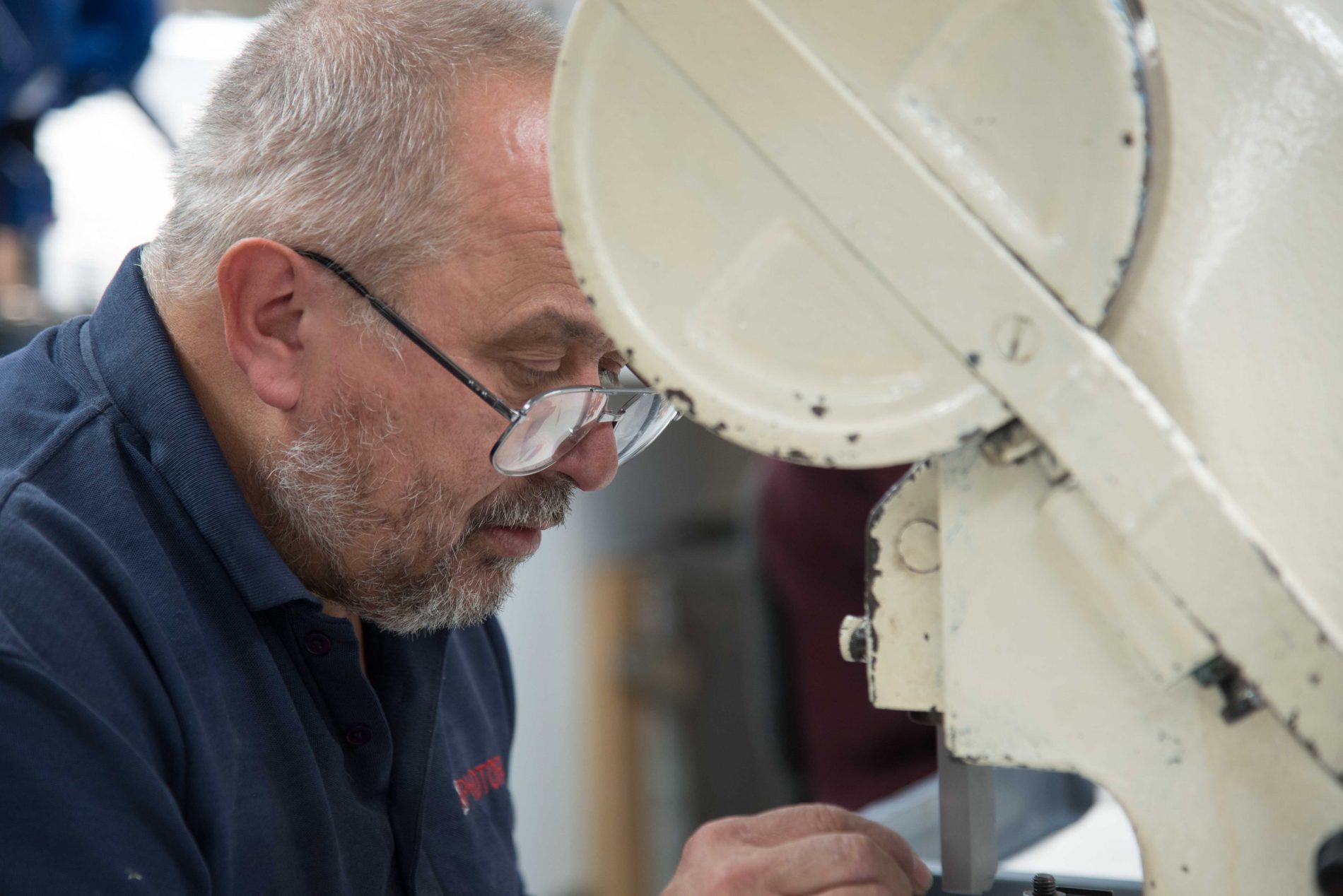
To cope with the flexibility of such a sector, it is likely that components are subject to change. This is why prototyping is such a sought-after service, and one that Photofab proudly provides. This means that product developers are free to amend their requirements until the right design is found, rather than rushing in with one design and hoping it works, saving on not just costs, but valuable time.
Once Photofab makes a prototype, the volume production process gets underway, with Photofab conforming to the latest quality and environmental standards. Once again, Photofab’s experience serves it well as it produces only the highest quality product with minimal environmental impact.
Keeping it clean
As covered in the most recent blog post on renewable energy, Photofab contributes greatly to the production of fuel cell plate technology. These plates are used as an alternative to batteries, but they do not run down or need to be recharged. They are also not just being used in cars, but everything from aeroplanes to even your boiler! However, the automotive sector changes so much that we can’t even be sure that hydrogen fuel cells are the way forwards. Something else may be just around the corner.
Nevertheless, one area that hydrogen fuel cells remain prevalent is construction vehicles. There have been many heavy machines from manufacturers such as JCB who now solely operate on hydrogen, as companies aim to meet their targets for zero carbon emissions. For example, hydrogen engines were initially trialled by JCB on excavators, a vehicle type that puts far greater demands on engines than trucks or cars do. Following a successful run, JCB workers felt that this indicated hydrogen engines would be suitable for a wider range of vehicles, and this may be rolled out.
If electrification proves to not be enough for such construction vehicles, as they will have to go through a recharge period in order to operate, Photofab’s role will remain crucial as it continues to play a vital role in the supply chain for hydrogen fuel cells. Stage V diesel engines may have paved the way for clearing harmful emissions, but hydrogen fuel cells can ensure a fully clean operation.
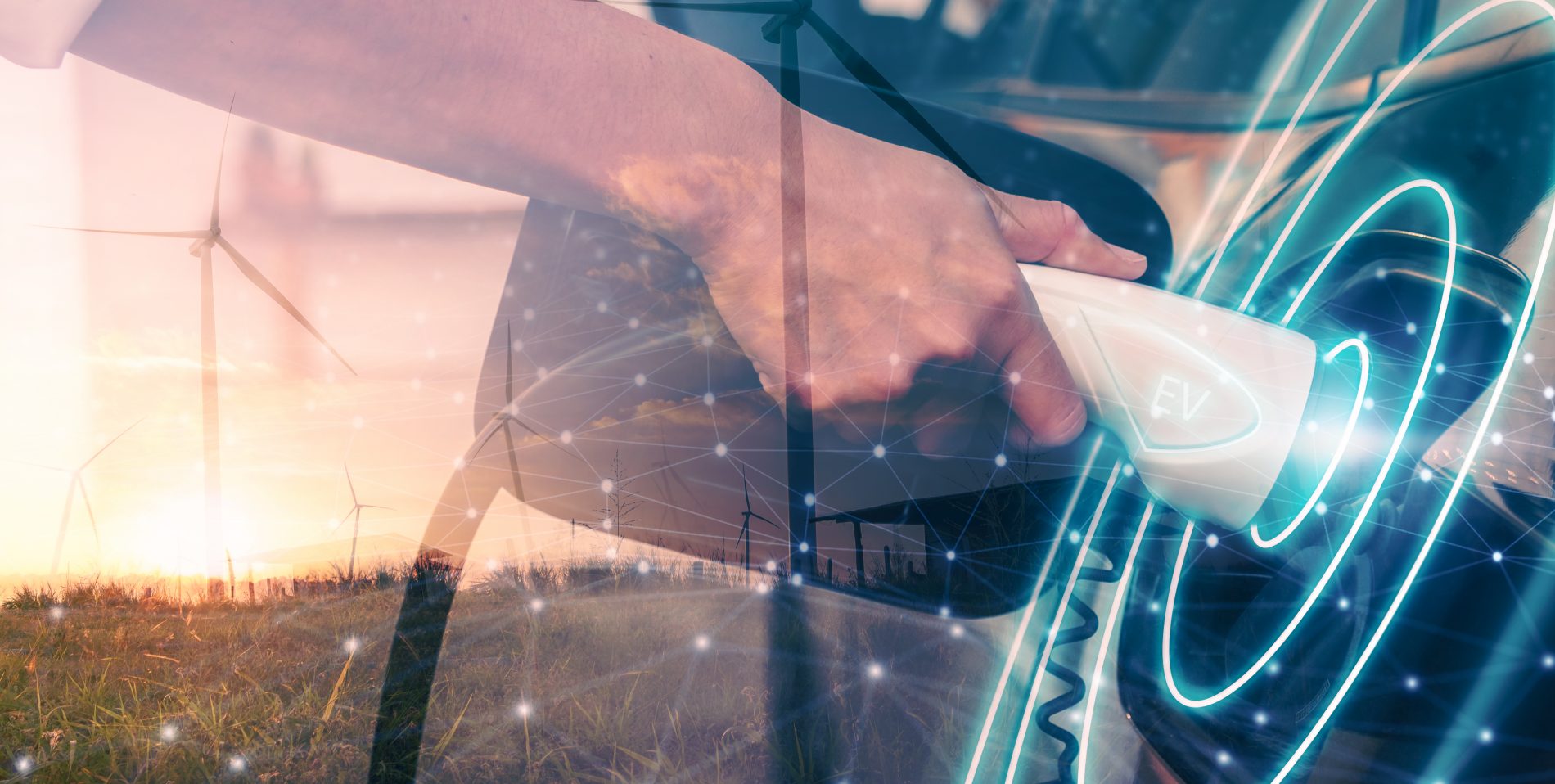
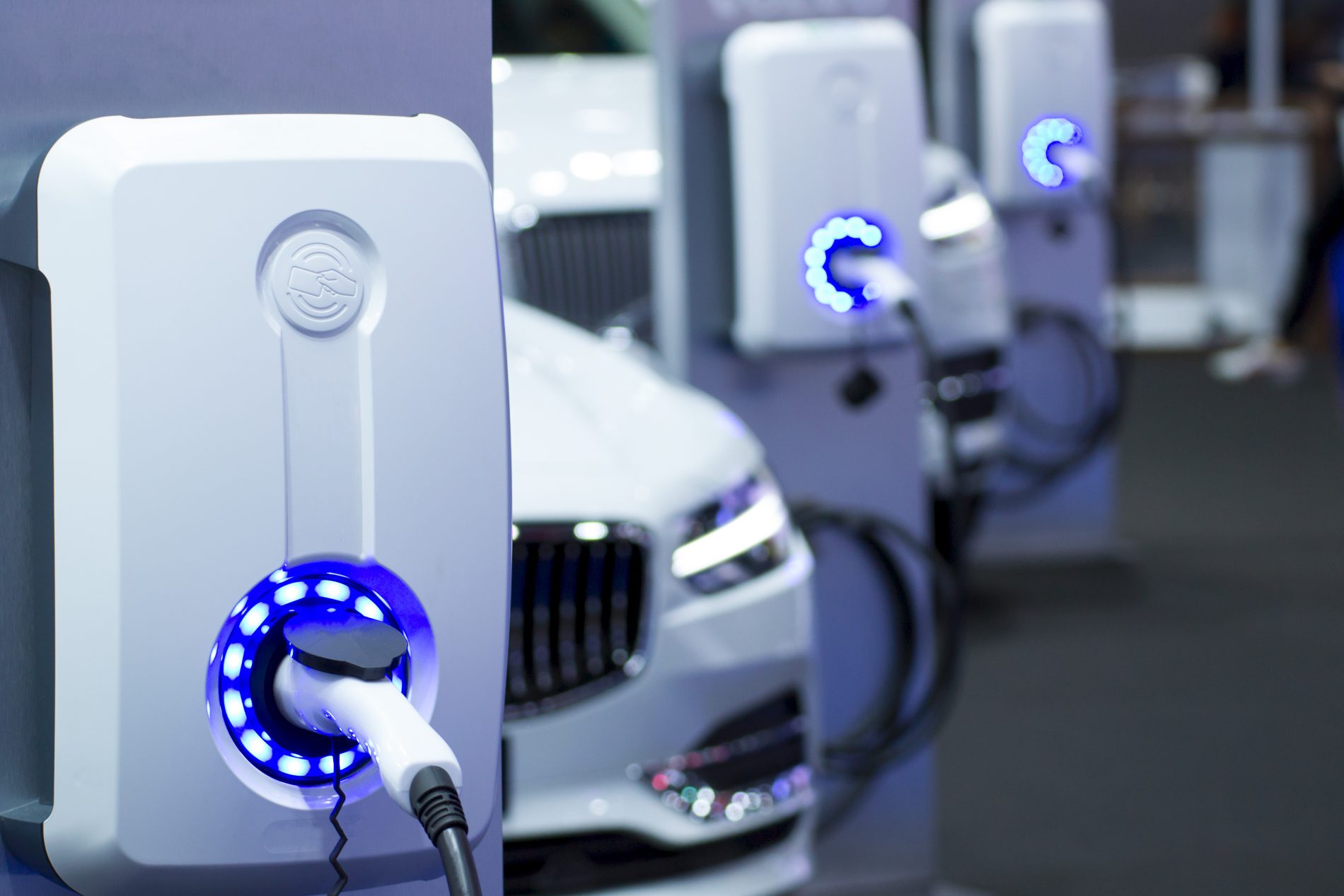
A fork in the road ahead
The future of car manufacturing looks set to change dramatically, and if trends are to continue, on-road vehicles may very well be driving themselves in the coming years. This means that focus will shift more to what the interior of these vehicles will look like, as opposed to the exterior design.
An example of the exterior production process becoming greatly automated has been the Giga Press casting machines being used by Tesla, which turns 70 individual parts into one giant part, simplifying the production line. For the more precise individual components, Photofab’s capabilities are ideal for the manufacture of small, intricate parts within the vehicle, including etching channels, which involves removing channels of metal to allow for the flow of hydrogen/air; all completed meticulously with full accuracy. Who knows what we will be using inside cars soon? If it becomes a mobile office, like many have predicted, the possibilities could be endless, and Photofab will continue to be in the driving seat.
Photofab provides experienced engineers and dedicated account managers to all customers, enhancing the customer experience and keeping them up to date during the project, with account managers providing advice throughout. Together with its customers, Photofab will help the automotive industry reach unfathomable heights.
To engage with Photofab on your next project and benefit from reduced lead times and costs, a rapid prototyping service and decades of industry know-how, use the contact page to tell Photofab what you need and see just how quickly the team respond!
For more stories like this, follow Photofab on LinkedIn and Twitter.