Keeping the communications industry connected
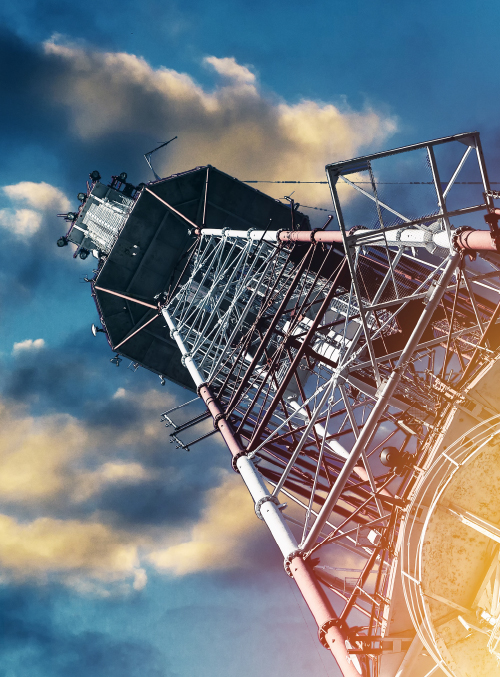
The evolution of communications and the products and devices entering the market has been monumental in recent years. Smarter technology has come to the forefront and started to shape our lives.
With it comes increasingly diverse challenges around the miniaturisation of devices and the components within them. Reliability is also a very important requisite as consumers demand longer battery life, more robust builds, and easier portability.
Components get smaller, more intricate, and more precise with every evolution of the latest smartphone, tablet, or communications device, not to mention the components for associated accessories such as microphones and headphones.
The one thing manufacturers in this field will be keen to know is whether the metal components required for such devices can evolve at the same speed.
Rising to the communications challenge
Whilst the communications industry moves at pace, so does the competency of chemical milling. That’s why Photofab often recommends the technique for component requirements in this sector. The technique allows for the highly accurate production of parts which is paramount for an industry demanding strict requirements on tight tolerances.
With the technique satisfying the desire for micron-accuracy, the next challenge is ensuring that components meet the quality measures undertaken during inspection. Photofab delivers a burr-free and stress-free manufacturing method from prototype components through to volume production, always preserving the original properties of the metal.
This dedication to producing quality components remains no matter how complex the requirement, and the communications industry can be very demanding on quality and complexity, whilst also instructing on diverse specifications for material selection and finishes.
Chemical milling is again the technique to satisfy these demands, with the ability to provide formed, heat treated, plated, and assembled components in a selection of metals and surface finishes. Because of the flexibility of the process, it is the preferred option when compared with more traditional metal working processes.
Talking of flexibility, component designs are likely to change when it comes to communication devices, so a fast and agile prototyping service is often required. Product developers are given the confidence to test and adjust until the right design is fixed when they utilise Photofab’s prototyping service. And costs will remain much lower compared with alternative techniques that would require much lengthier mechanical tooling adjustments. Chemical milling has proven to be an effective method of manufacturing, considering the various challenges that miniaturisation has thrown up, but there’s always new technology posing new challenges just around the corner.
From small to sensory
Miniaturisation is no new trend. Things have been getting smaller and smaller for decades and staying ahead of the curve as a component supplier has been key to Photofab’s success in the industry throughout its 50+ years.
The next industry evolution has been a long time in the making and in many ways is still waiting for its breakthrough moment. That evolution is in haptic technology. This technology is applied to devices that allow a user to have an experience through their sense of touch.
You’ll already be aware of haptic technology in its most common interpretation – the use of vibration in mobile phones is perhaps the best example to illustrate it.
It is a combination of tiny metal components vibrating beneath the surface of touch screens, pads and buttons that deliver the feedback to your finger as you type out a text message on an iPhone’s touchscreen keyboard or feel that sensation of clicking a button as you rest your thumb on a touch sensitive pad.
Smartphones and similar communication devices are often quick to adopt new technology like haptics and it is vital that the process of chemical milling and etching evolves at the same speed, because staying ahead in one industry allows for opportunities in others.

The small components needed to deliver unique user experiences in smartphones will also be adopted in video game technology, electronic displays and personal computers, virtual reality devices, simulators and robotics, as well across numerous applications in industries such as automotive, aerospace, defence and medical.
What’s definite and exciting is that haptics is here to stay and as it evolves, it will add another dimension to our digital lives. Photofab plans to come along for the ride.
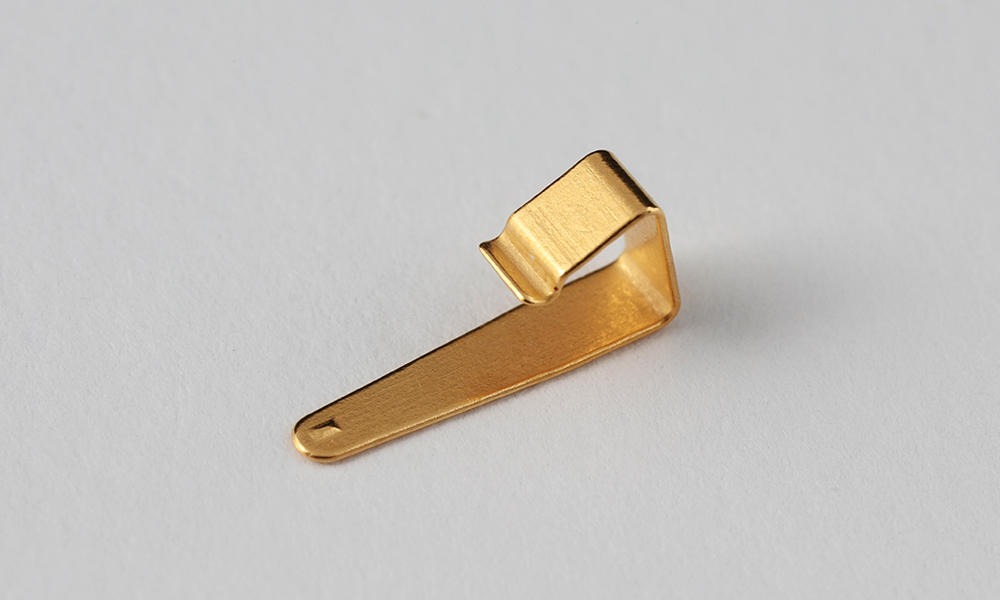
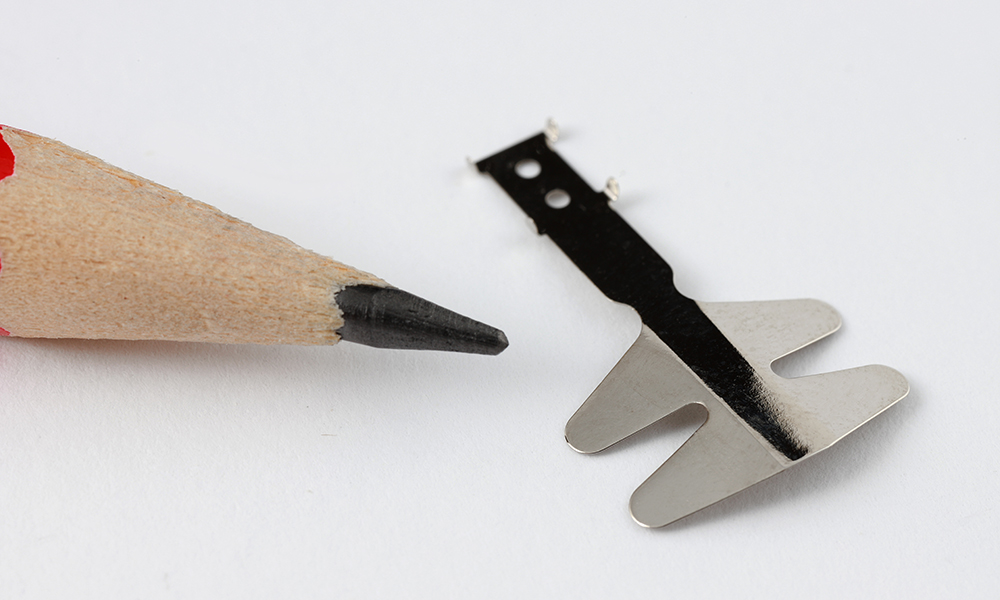
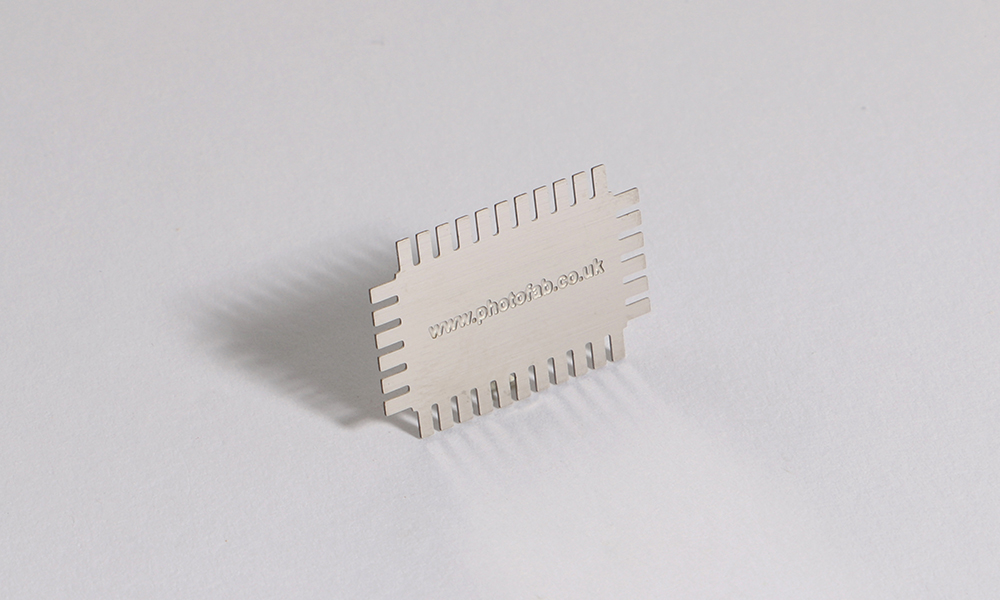
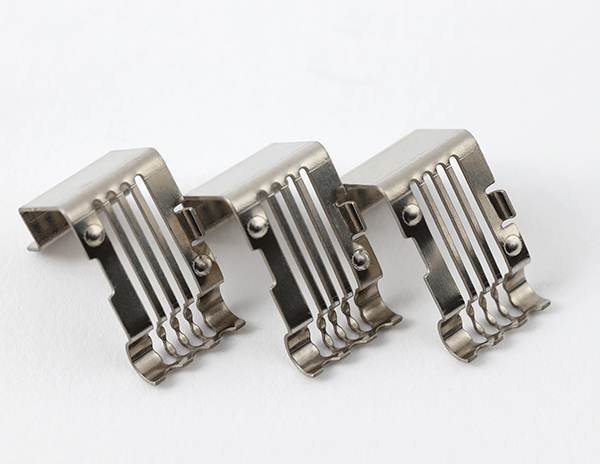
Friendly experts ready to talk
Many companies choose Photofab because they know they’ll benefit from experienced engineers and dedicated account managers. Account managers will help with product development by offering advice on best manufacturing processes to enable the product to be manufactured economically, be it at concept stage or volume production.
To engage with Photofab on your next project and benefit from reduced lead times and costs, a rapid prototyping service and decades of industry know-how, use the contact page to tell Photofab what you need and see just how quickly the team respond!
For more stories like this, follow Photofab on LinkedIn and Twitter.