Photofab can supply EMI / RFI Shielding cans and solutions using various intelligent design techniques. For over 50 years, Photofab have worked closely with leading electrical and electronic manufacturers to adapt and perfect our processes, ensuring the highest standards in quality, precision, and consistency for the manufacture of EMI/RFI Shielding products.
Shielding is a smart, simple technique for controlling Electro-Magnetic or Radio Frequency interference. Shielding cans are metal boxes that are applied to the board with clips or solder. Photofab has experience in producing these shields. These shields are most commonly applied to parts of a circuit that have high EMI emissions or are sensitive to inference.
By shielding, the component is protected and can function as intended. With the use of a shielding box or can, EMI performance levels can be achieved that would otherwise be far more difficult and costly to achieve at a product enclosure level. Photofab offers an effective, cost-efficient solution with its EMI shields, which also enable simple maintenance.
Shielding or screening cans are commonly manufactured in Nickel Silver, as it maintains solderability with no post coating required, or traditionally in either brass or mild steel plated with either tin or nickel, depending on what suits your application best. The full process is available, including forming, plating, soldering and / or spot welding.
For more information on how we can reduce your costs & improve lead time contact our dedicated account managers on 01480 226699 or email enquiries@photofab.co.uk.
FEATURES OF EMI / RFI PRODUCTS that can be achieved through Chemical Etching
Solder Joints
Butt jointed corners with tin plate finish, allows corners to be soldered for increased screening, where frequency dictates.
Spot Welding
Overlapping joint corners with tin plate finish are spot welded for increased screening, where frequency requirements dictate.
Locking Tabs / Locating Holes
an alternative to soldering, allowing greater rigidity depending on the needs of the application.
Dividers
provide discreet screening within the frame.
Holes / Cut Outs
can be incorporated as requested, at no additional cost.
Anti-Solder Migration Barrier
prevents solder creepage up the sides of its PCB mounting screening enclosures during automated and reflow soldering processes.
Spring Fingered Lids
easy access and excellent attenuation – our in-house designed spring fingered lids come from standard tooling and provide easy access and excellent attenuation.
Push Fit Lids
easy access and good attenuation.
PCB Locations
lancings or brackets can be specified to act as guides or supports.
Locking Pins
for exact positioning and retention, deal for reflow soldering applications.
Half Etch Pins
pins that are easily bent, to lock the shielding can into place.
Common Metal Types
Copper, Brass, Mild Steel, Stainless Steel, Nickel Silver and Mu Metal.
Common Plating Types
Tin plate (Bright and Electrolytic) and Nickel plate.
RoHs Compliance
All standard metal used for shielding cans are RoHS compliant. The types of plating we offer will always be RoHS compliant, unless you state otherwise. Please note that Hot Tin Dip is not RoHS compliant.
The Benefits of EMI / RFI Shielding at PCB Level
EMI / RFI Shielding at PCB board level is a deceptively simple technique for controlling EMI (Electro-Magnetic Interference). It is perhaps the most common technique to keep harmful interference out and also unwanted emission in. EMI Shielding at PCB level is simple to engineer with low cost. Board level shielding solutions can be used to achieve an EMI performance that would be far more difficult and costly at product enclosure level.
At board level, shielding cans can be used selectively on problem areas of a circuit, directly tackling components with emissions that are too high or are too sensitive.
In brief, PCB shielding cans are simple metal boxes that are easily soldered in place. Dealing with EMC problems at this level, ensures component and assembly costs are low and the appearance and ease of maintenance of the product are not compromised.
Solutions at product enclosure level – Why this is inferior
Practical EMI shielding requires considerable engineering skill to give good results. However, at product enclosure level, it can be complex and expensive when considering both additional material and assembly costs. Also, effective enclosure shielding usually requires substantial filtering of all cables, which pass out of the product right at the point where they penetrate the enclosure shield.
Shielding at PCB Level
Simple to engineer
Low-cost
High EMI performance achievable
Tackle problematic components directly
Shielding a Product Enclosure Level
Considerable engineering required
High Cost due to complexity
Additional materials required
Filtering for cables required
Effect on emissions
With the PCB shielding method of execution, the circuit board tracking and wiring is shielded inside the can solution. Due to space, contained tracks and wires are consequently very short and not very efficient as aerial radiating RFI or EMI. Furthermore, filtering to reduce overall emissions to an acceptable level, may be minimal if required at all.
DEDICATED engineering
Photofab understands the importance of skilled engineering when designing components and putting them into production. Therefore, we have heavily invested in a dedicated secondary engineering unit, the aim of this is to offer an even greater service and flexibility to our customers.
Originally set up to provide an in-house solution to support the etching division, it has proven so popular with our customers that Photofab are now offering toolroom, forming and finishing as stand-alone services. This means our customers now have access to a new level of flexibility – enjoying the convenience of full-service manufacture or pick and choose services to suit them. It truly is a complete service from Photofab.
Photofab continues to offer cutting-edge services and outstanding lead times, and we can do so because of continuous investment in our people and our processes, leading to class-leading output and lead times – including our rapid 24 hour turnaround service.
The benefits of
working with us
We are world leaders in the development of photochemical technology to produce intricately shaped components. We have produced over 80,000 different components over the years and are highly regarded for our chemical etching process. Our engineers offer many services that you can find here, and will offer advice to improve the product and reduce the costs.
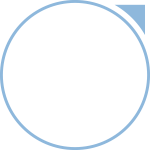
24-hour quotation service
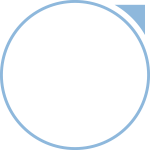
Dedicated account managers
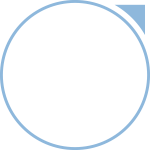
Rapid manufacturing service
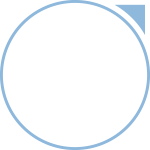
Cost saving stock of uni-tooling
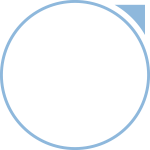
Etched fold lines for tool-free forming
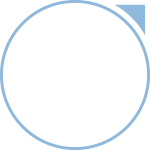
Full manufacturing service and supply chain management
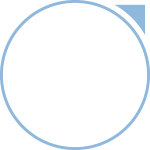
Access to manufacturing and technical advice and expertise
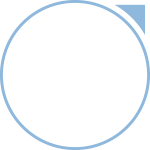
Quality accredited to ISO 9001, ISO 14001, ISO 45001 and SC21 Bronze
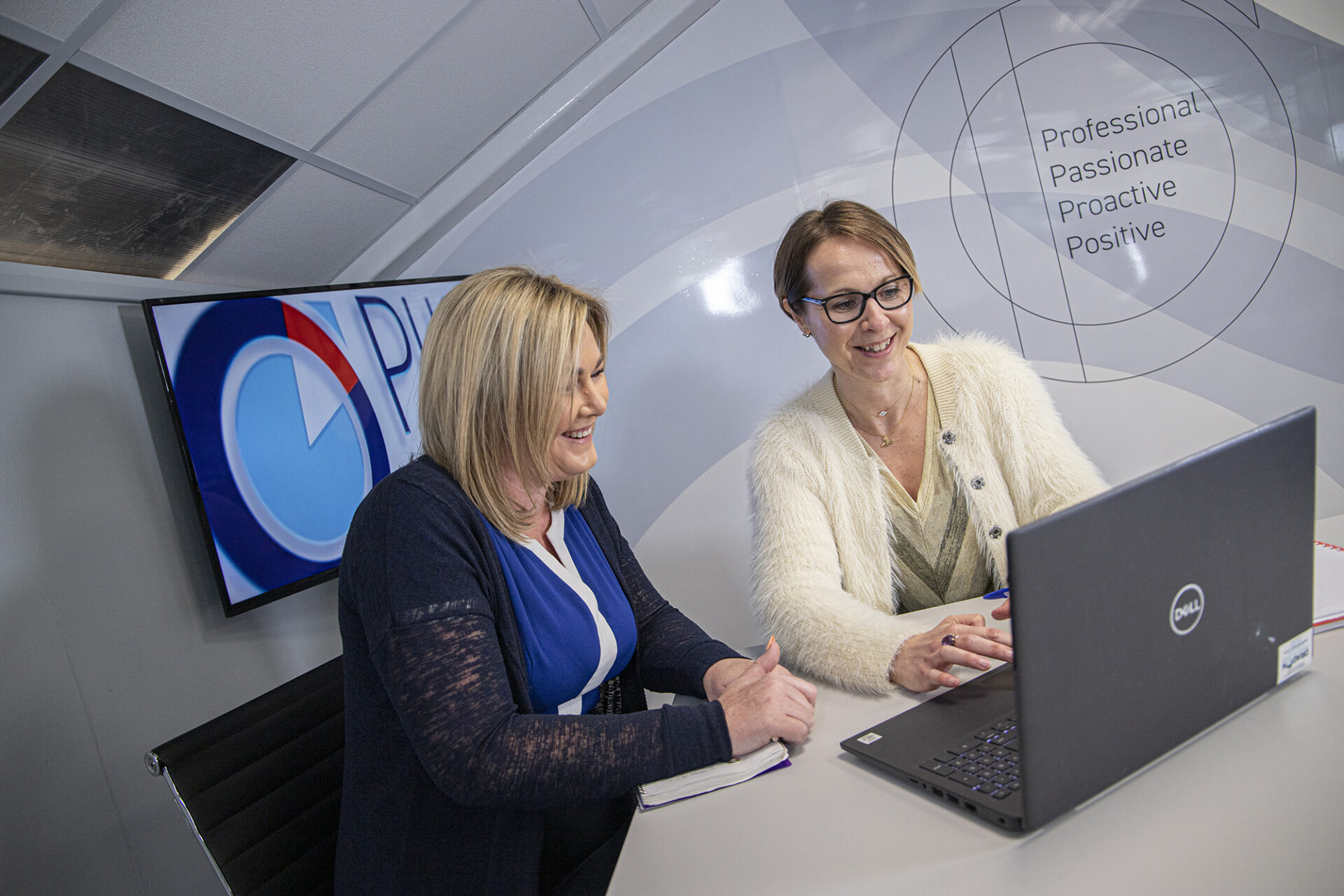
The Photofab difference
One of the key reasons Photofab enjoy its customer retention and longevity is the team of dedicated account managers. This ‘single point of contact’ throughout the whole process, ensures a personal service, and pride in the quality and reliability of the entire Photofab service.
Customers rely on their dedicated contacts’ understanding and in-depth knowledge of their specific requirements and know the highest standards will always be met using the most efficient and cost-effective methods.
This consistent service is the foundation of our customer loyalty and is maintained throughout every department and every stage of production. Put us to the test for your next project and call one of our account managers on 01480 226699 or use our customer enquiry form.
start your production journey today
If you are looking to find a complete service include dedicated engineering to design and implement your solution, get in touch with us. You’ll be allocated your own dedicated account manager who is always on hand to advise and take care of everything for you. Call Photofab on 01480 226699 or contact us now to see how Photofab can add an extra dimension to your manufacturing project. Keep up to date by following us on LinkedIn and Twitter.
TAKE A LOOK AT OTHER
PRODUCTS FROM PHOTOFAB
To find out how we can help you
Get in touch today
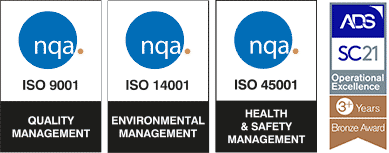