Since 1968, we have specialised in precision chemical etching of metals, building a reputation as the world leaders through exceptional customer service, lead-times and quality management of chemical etching and value-added services. Customers rely on our experience and technical expertise to ensure the highest quality production is maintained. We utilise the most efficient and reliable processes to maintain our bronze awarded SC21 accreditation and 98.5% On Time Delivery record.
All of our processes follow SC21, ISO9001, 14001 and 45001 with full traceability along the way. Our experience, coupled with our vast range of industry leading equipment and trusted network of partners makes us the perfect choice for precision manufacturing, whatever your requirements.
For more information on how we can reduce your costs & improve lead time contact our dedicated account managers on 01480 226699 or email enquiries@photofab.co.uk.
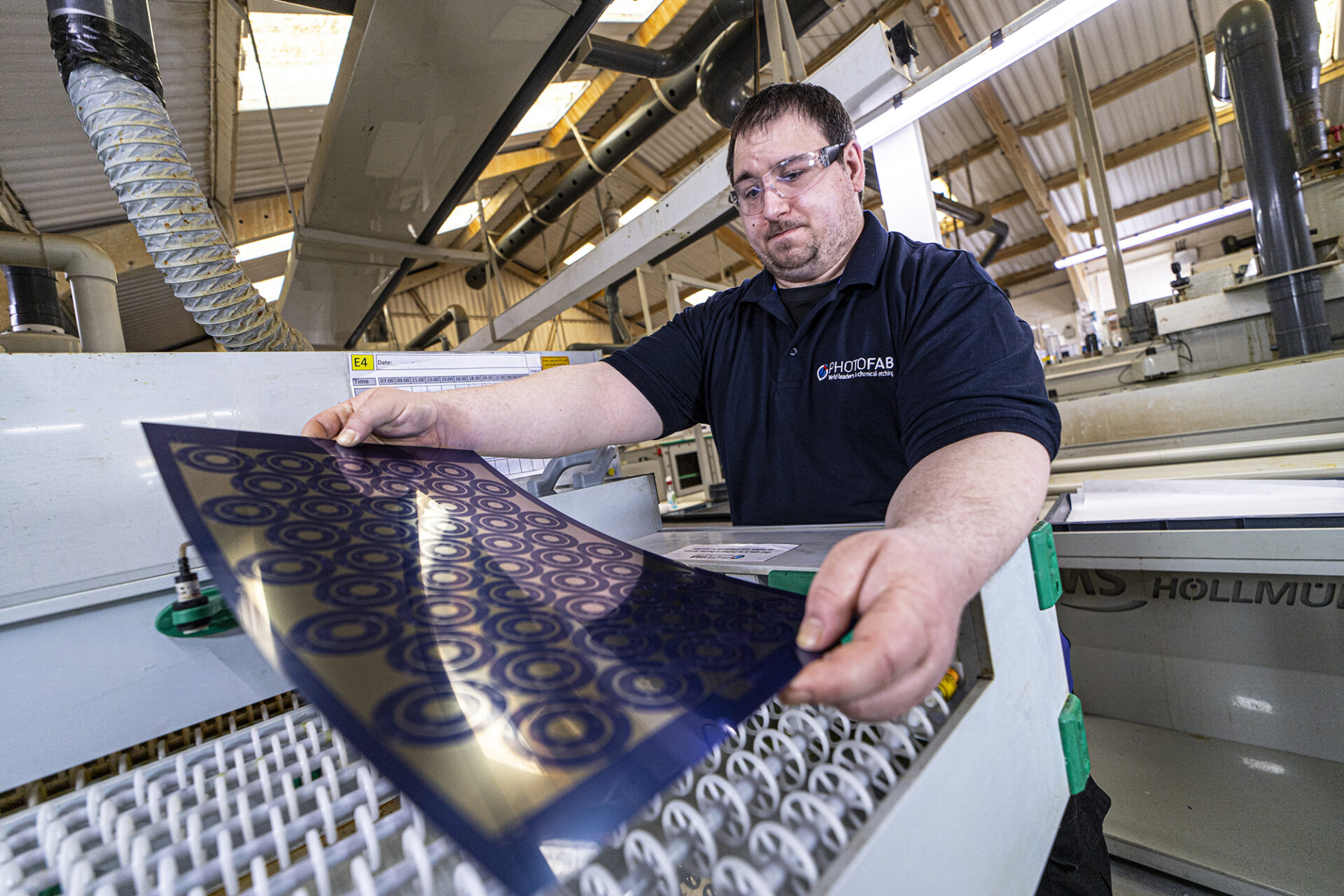
What are the benefits of our chemical etching service?
- Fast prototyping
- Rapid 24hr quoting
- Short lead times
- Product Realisation support team
- Large stock of industry standard metals
- Low-cost manufacturing process
- Technically trained dedicated account managers
- Low-cost digital tooling
- Low-cost digital tooling design changes
- Mixed sheet graphic tools for prototypes to full production
- Vast range of metals can be etched
- Etching to Micron accuracy
- Extremely tight tolerances offered
- Half Etched fold lines for tool-free forming
- Half-etched forming to tight tolerances
- Metal properties unaltered by the etching process
- Logos can be etched into flat parts
- Tabbed-in components offered or loose
- No heat or force used in production that could distort parts
- Burr & stress-free process
- Blemish free finish
- As low as 0.010mm sheet thickness up to 1.2mm
- Heat treatment process available to harden metals
- Full hard tool forming service available
- Plating available
- Access to a vast collection of uni form tooling (save thousands and quicken lead times)
- Flat parts available in 24 hours
- Standard rapid service parts ready in 3 working days
- Sample packs available
- Seam Welding and spot welding available
- Quality accredited to ISO 9001, ISO 14001, ISO 45001 and SC21 Bronze
- Full manufacturing service and supply chain management
how does chemical etching work?
Chemical etching metal is a machining process which uses acids and other chemicals to dissolve exposed areas from a metal sheet to produce highly accurate components. A masking film is created from the design to protect the areas on both sides of the metal sheet, so only the exposed areas are etched. This process has incredible precision, removing anything from 10 microns (0.0004”) to over 0.5mm (0.020”) on both sides of the sheet simultaneously, creating a highly efficient and effective fabrication process. See our metal etching process sections for more information.
Metal etching is sometimes known as aluminium etching, ferric chloride etching, acid metal etching, chemical etching, or photo chemical etching. The range of metals possible is vast, from brass, copper, beryllium copper, to ferrous metals including stainless steel, carbon steel and mild steel, up to a thickness of 1.5mm. See our Materials section for a full list of metals that can be chemically etched.
For metal cutting over 1.5mm, up to 22mm, we can offer laser cutting, reassuringly managed and quality controlled by Photofab to the exact same high standards as our metal etching.
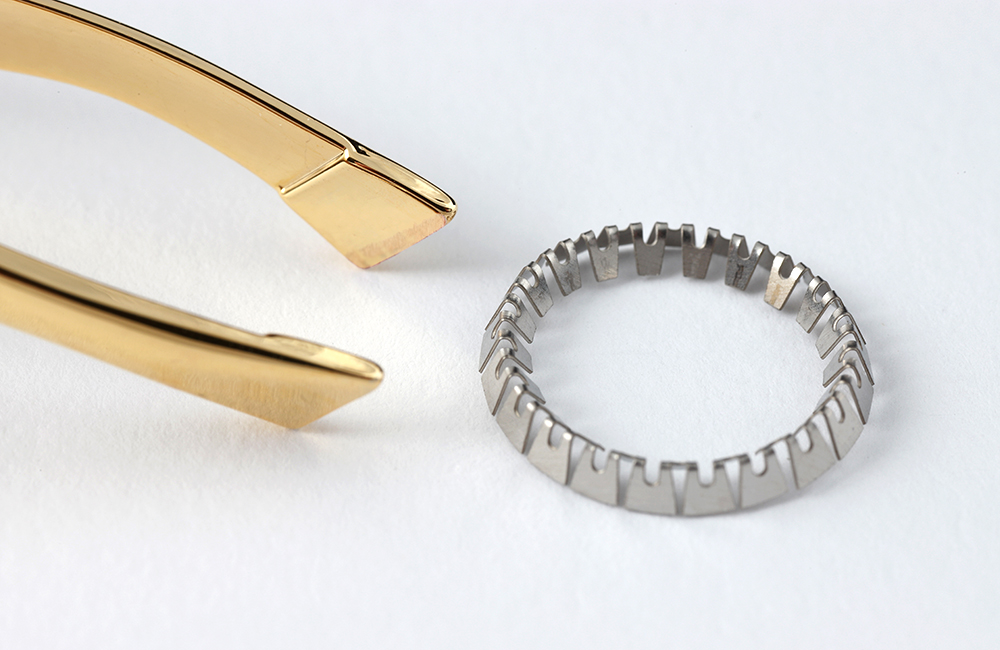
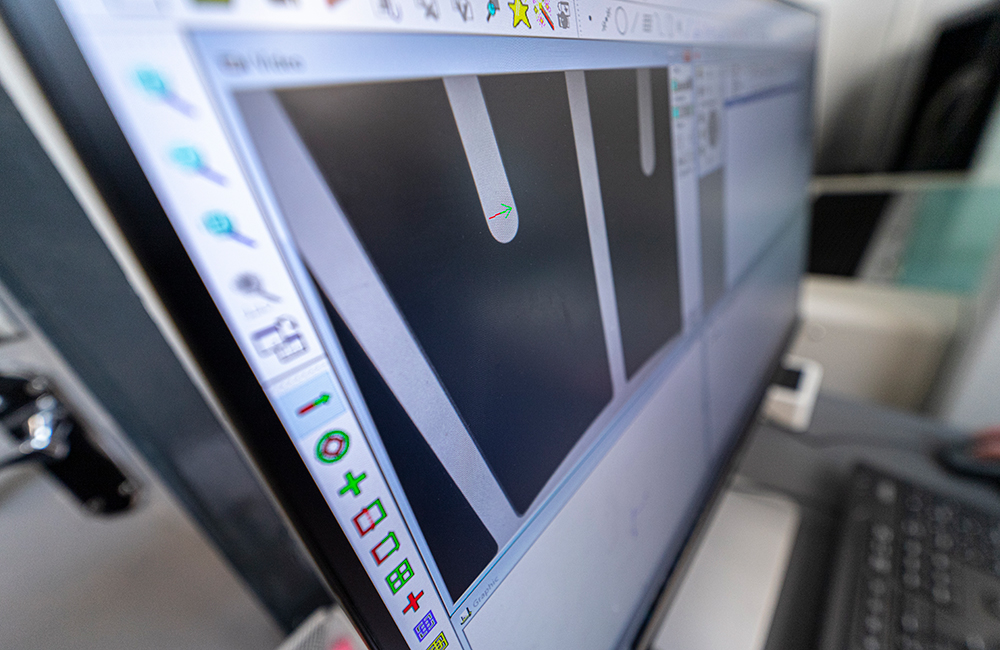
1. Design Advice
At all stages of the chemical etching process, our engineers will offer advice both to improve the product and reduce the costs. We are able to view all types of data; from sophisticated CAD files to rough sketches. Our metallurgist will advise you on the most suitable metal to use for your application. A wide range of metals and thicknesses are held in stock.
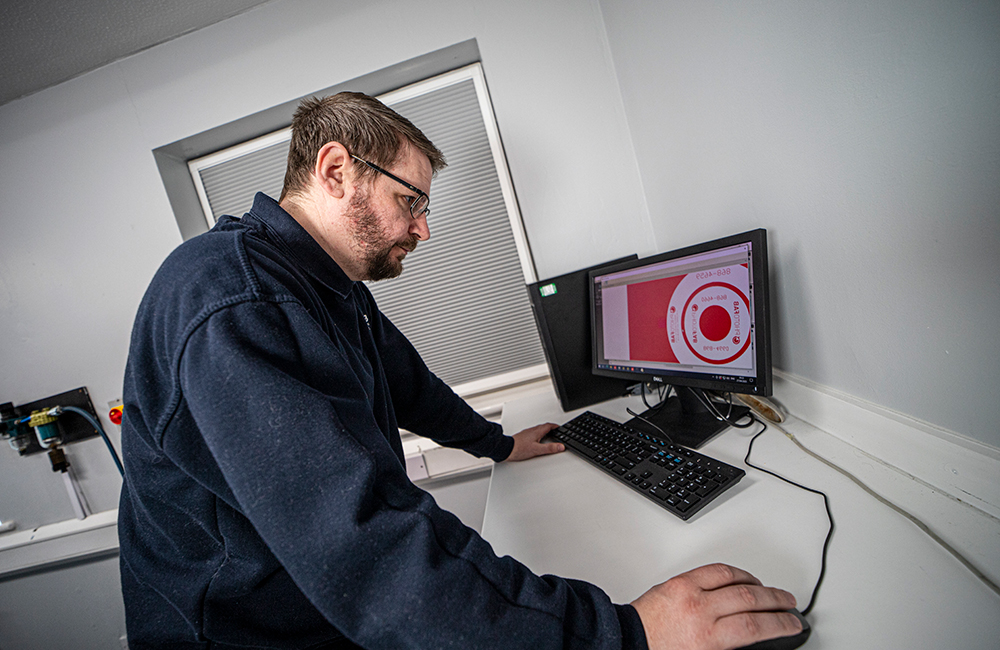
2. Receipt of Drawings
The customer sends data to us either in the form of a drawing or an electronic file. This is converted using CAD to allow for the etching compensation and “stepped and repeated” to fit as many components as possible onto the film.
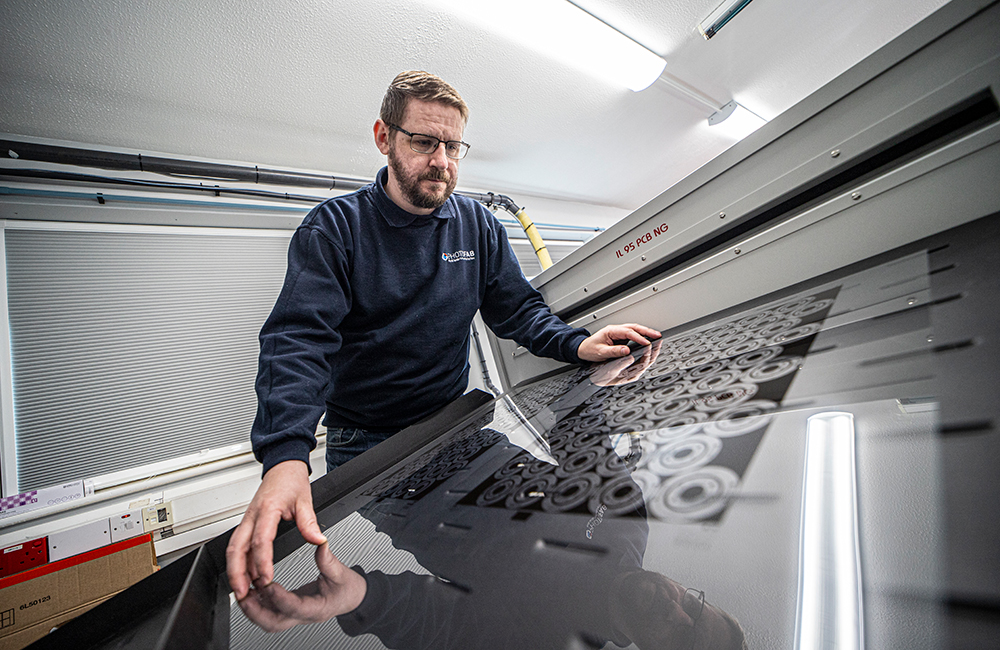
3. Film Plotting
This is then laser plotted to create the Graphic Tool. Two tools are prepared; one for each side of the metal, which allows etching from both sides. Variances between the two tools can facilitate “half-etching” from one side.
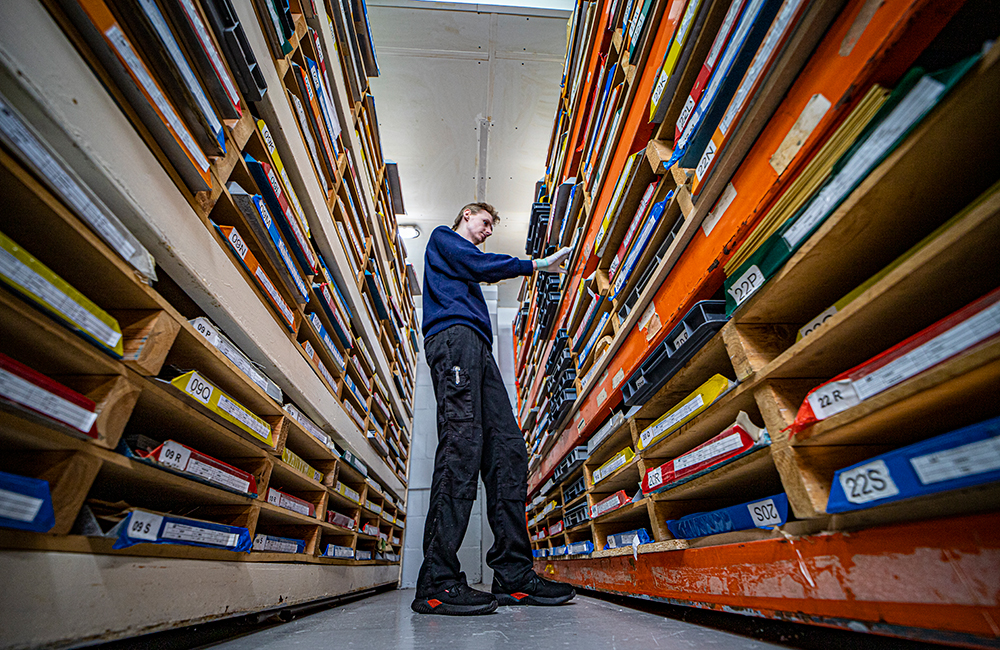
4. Metal Selection
We carefully review your drawing to ensure that the correct metal has been selected both from a performance and cost perspective. Full traceability is maintained on all grades of metal, certificates are available upon request.
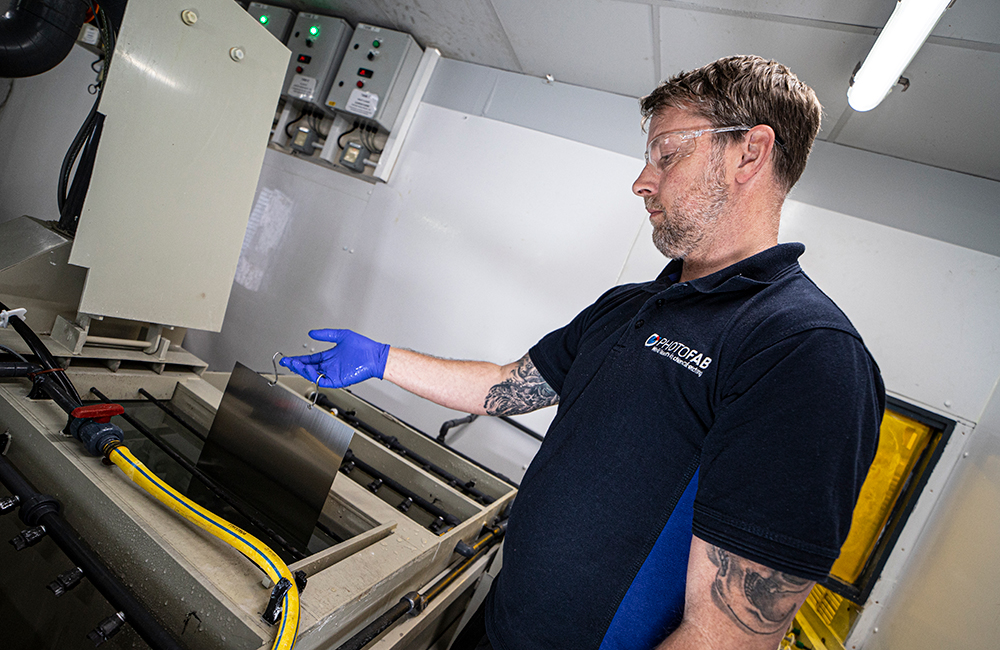
5. Metal Preparation
Before coating the metal with a photosensitive resist, the metal is thoroughly cleaned to remove all dirt, rust, greases and oils. This allows good adhesion to the photosensitive resist to be obtained.

6. Resist Lamination
Photosensitive resists are UV light-sensitive polymers which are applied as a dry film to the metal either by hot roller lamination. The type of process used depends on the metal being used and the type of subsequent processing required. The coating is applied to both sides of the metal.
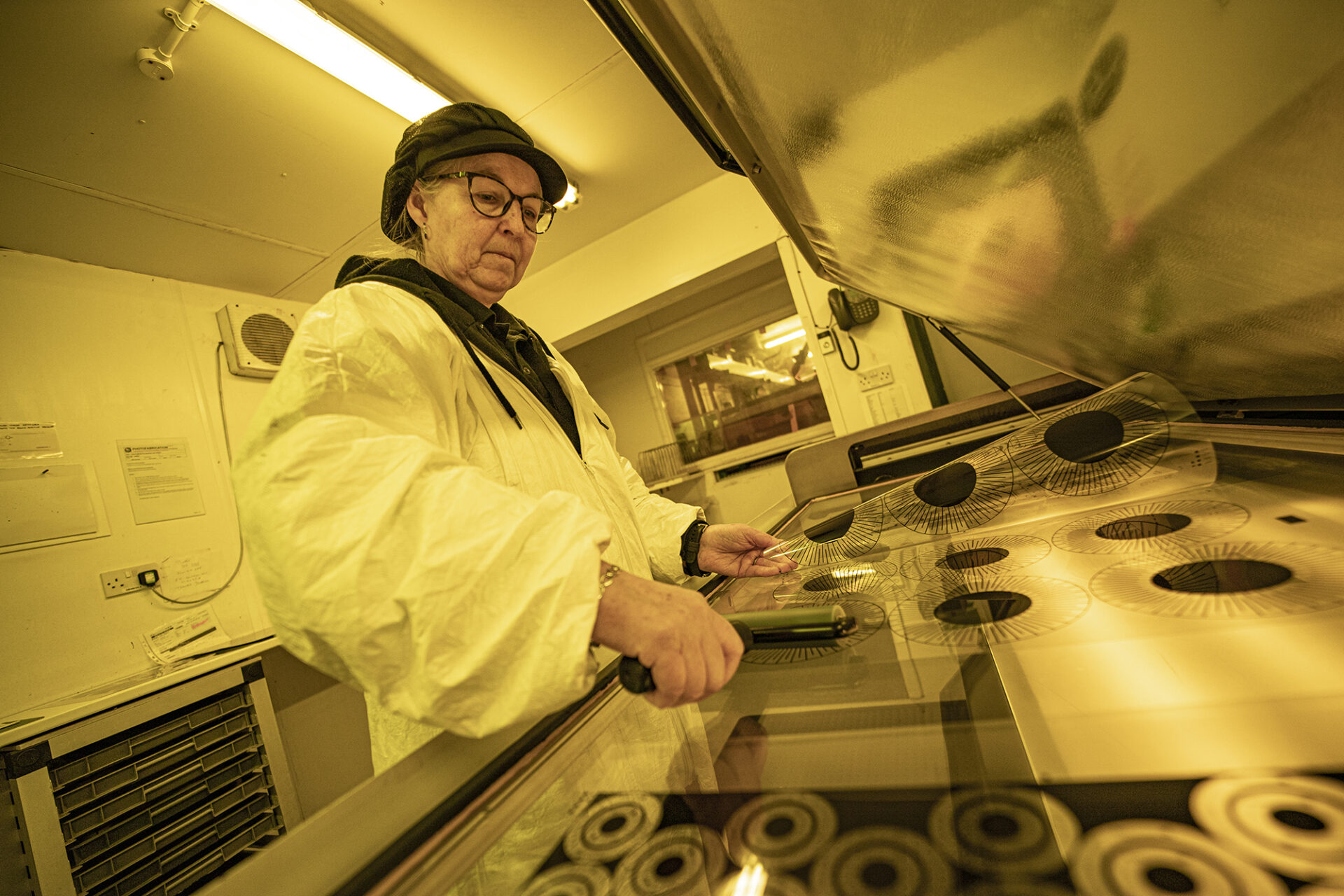
7. Printing
The Graphic Tool carrying the component image is now laid over both sides of the metal which has been previously coated with the photosensitive resist. The combination of Graphic Tool and coated metal is then exposed to UV light to transfer the image onto the metal coating.
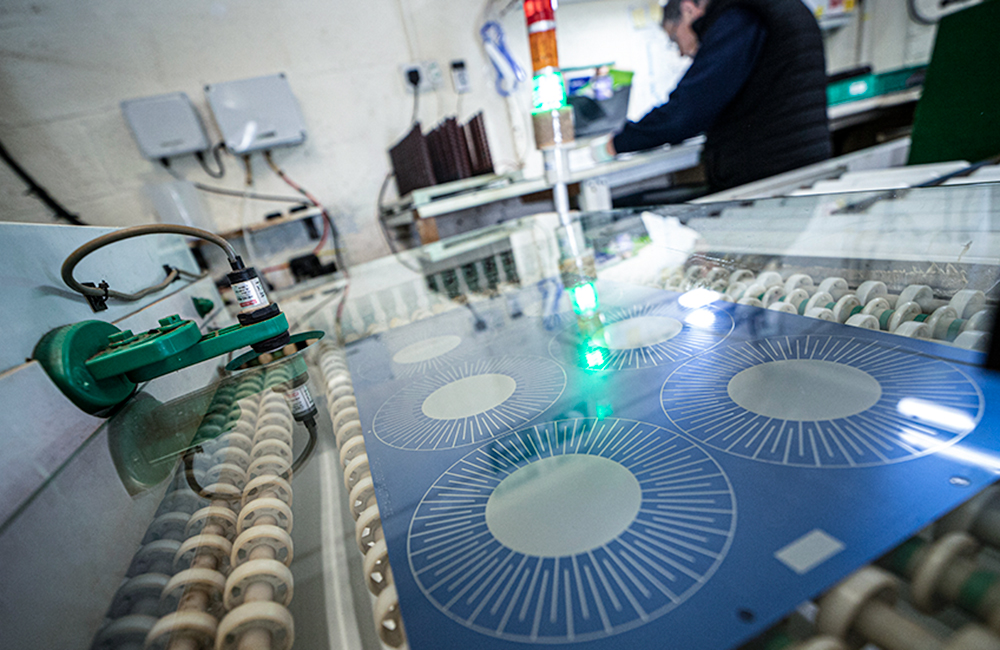
8. Developing
The area of photosensitive resist which has been protected from the UV light by the Graphic Tool, remains soft and is then chemically developed away leaving the metal exposed ready for etching. The component image remains protected by the resist.
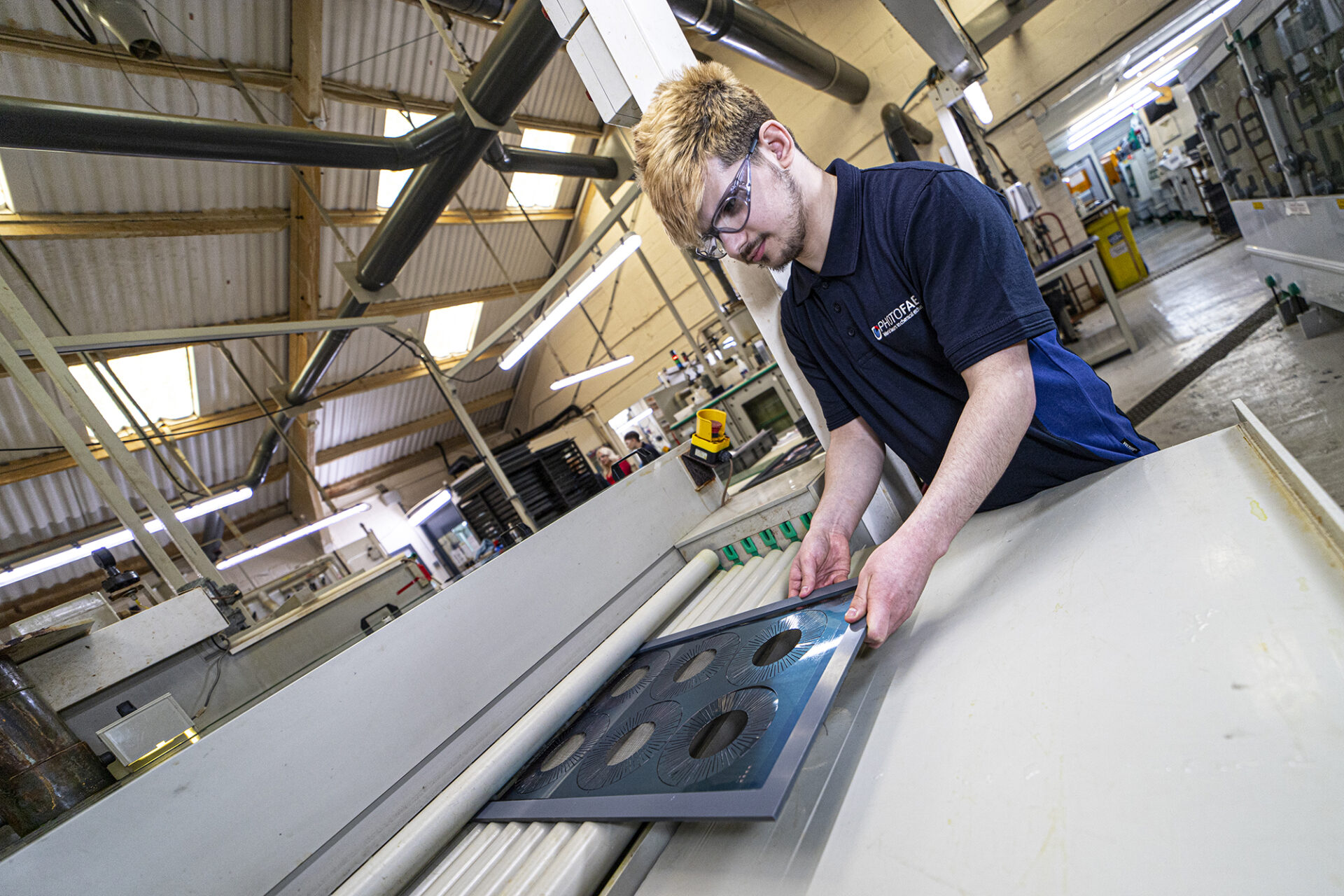
9. Etching
The prepared metal sheets are now passed through the etching machine to remove the exposed metal. Virtually all metals can be etched, although some are etched more readily than others. Photofab have developed bespoke chemistry for a range of materials allowing us to offer the highest quality. The etchant is regenerated to maintain a constant etch rate and lower environmental impact.
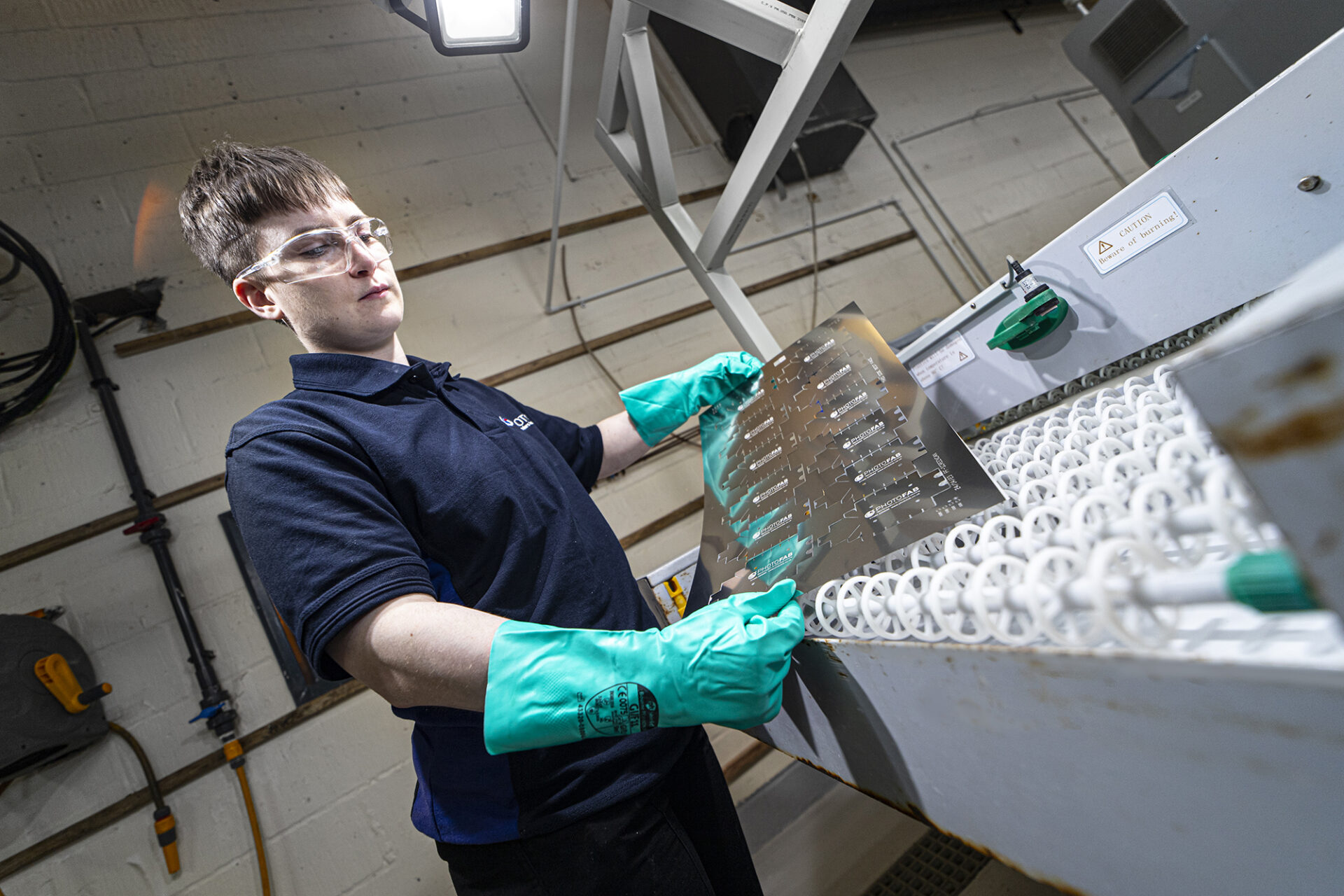
10. Stripping
The final process of PCM (Photo Chemical Milling) is to strip off the resist from the etched component and ensure that the metal is clean. A combination of automation and operator care is employed depending on the component specification.
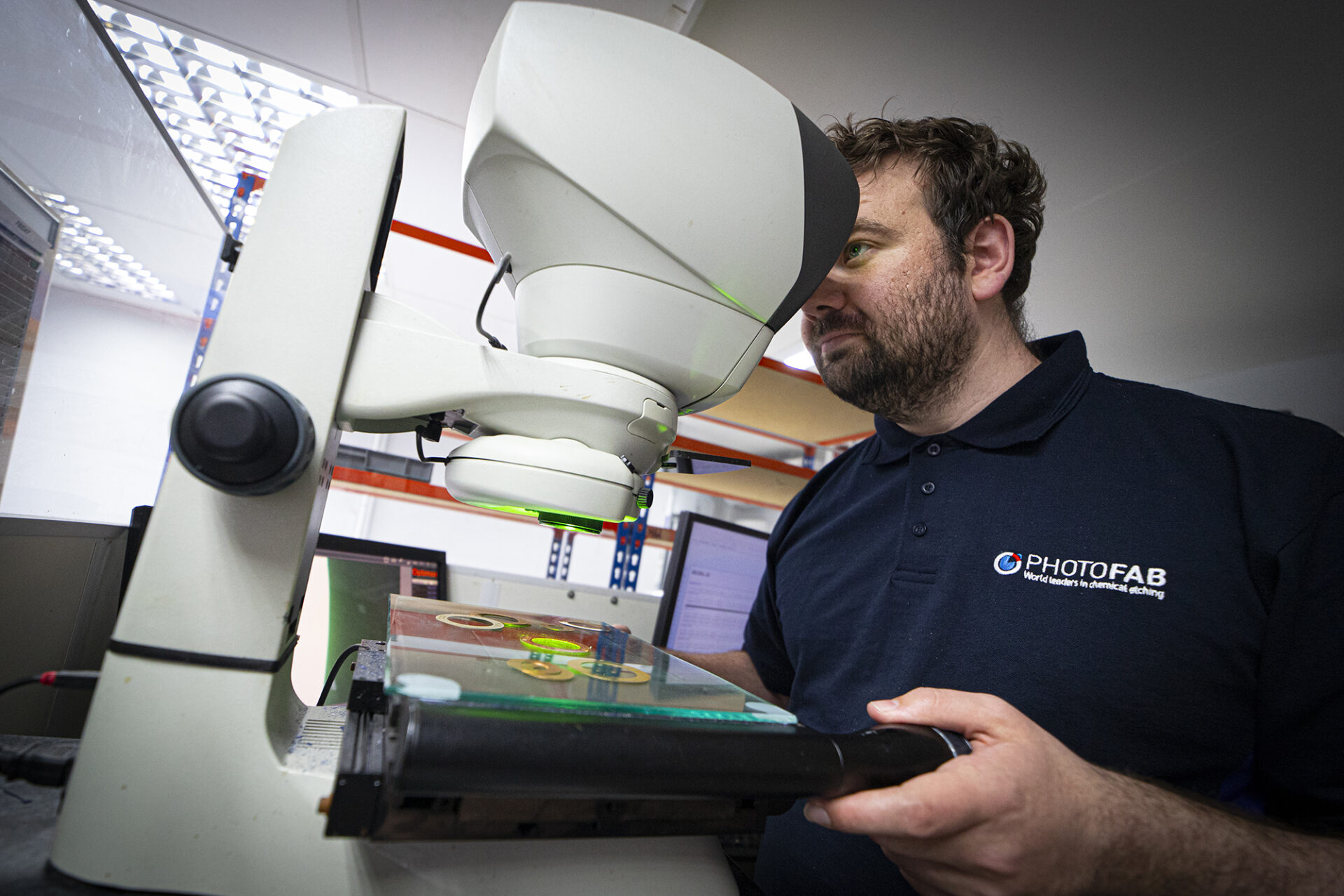
11. Inspection and Packing
The components are checked electronically to ensure they conform to dimensional specifications, and they are visually inspected for any surface defects. High quality finished products are then securely packed for overnight delivery.
Etching Tolerances
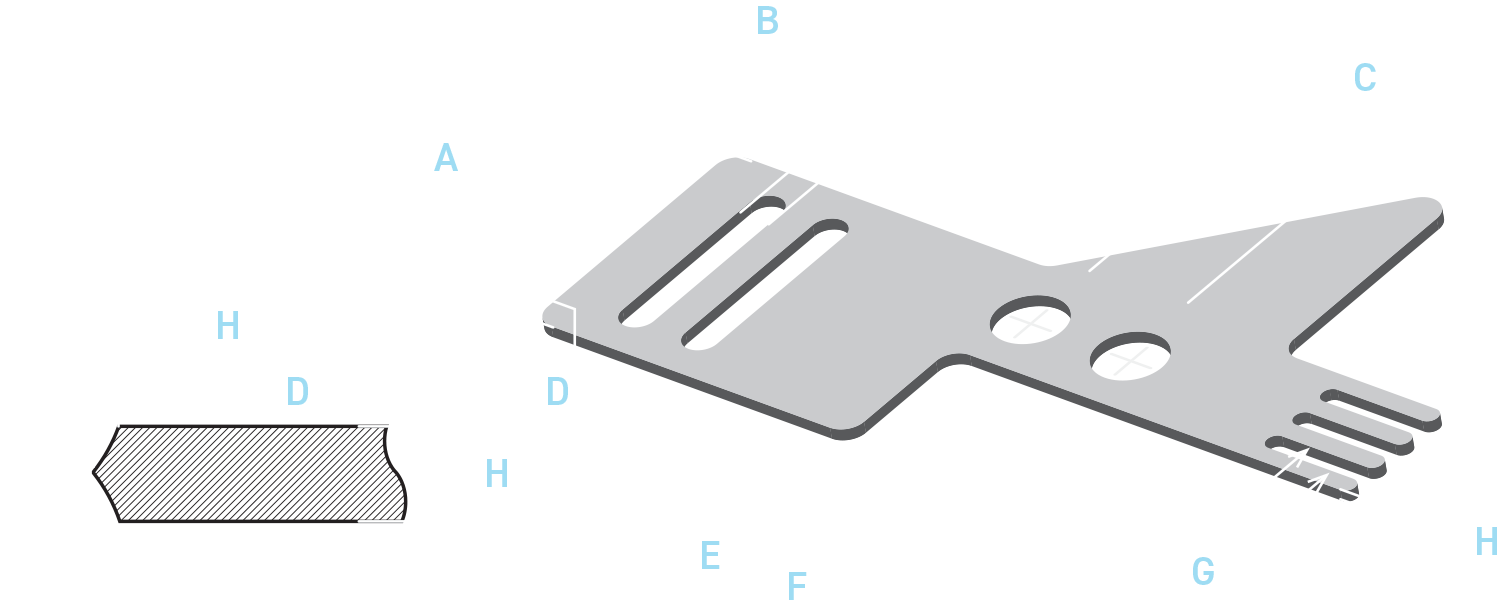
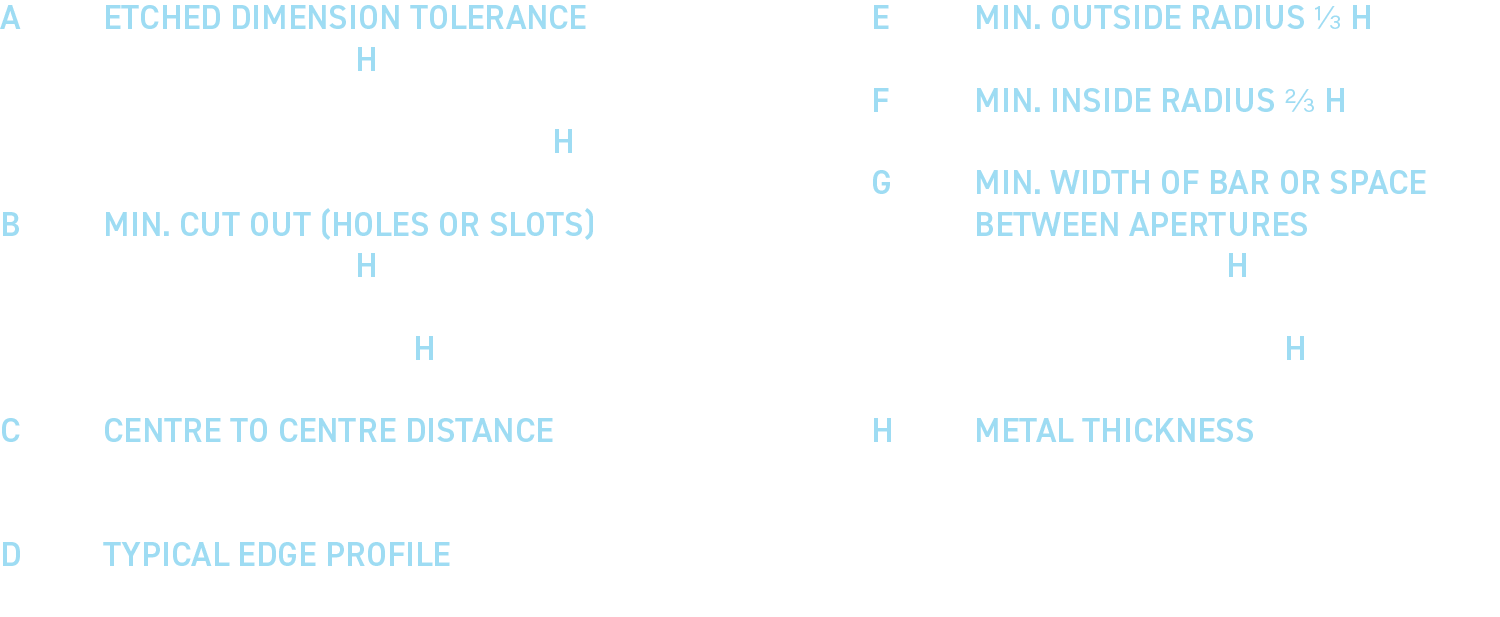
chemical etching services
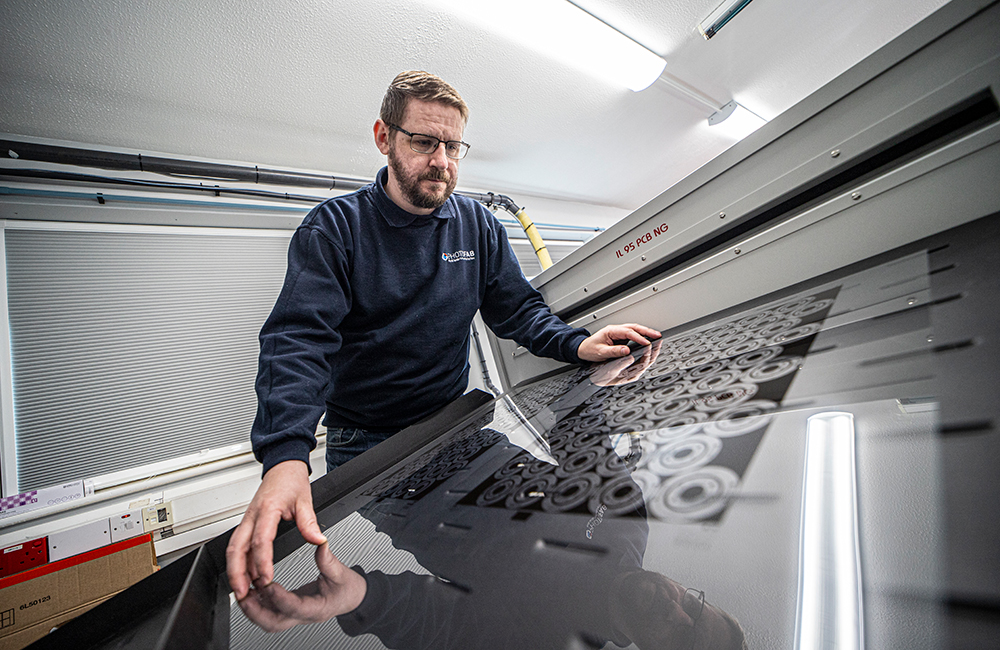
For prototyping
Prototyping is often a painstaking process of trial and error – even minuscule design changes can cost valuable time and money. Chemical etching drastically reduces the cost and time consumption of these experiments. Rapid prototyping is possible, ensuring that you can easily implement cost-effective improvements. See our Rapid Turnaround Service for more details.
Chemical etching bridges the gap between prototyping and full production, using the same tooling to make one part or a million. We’d be happy to discuss how we can bring your ideas to life, so you can see a return on your hard work. Send us your specification to get a quote within 24 hours.
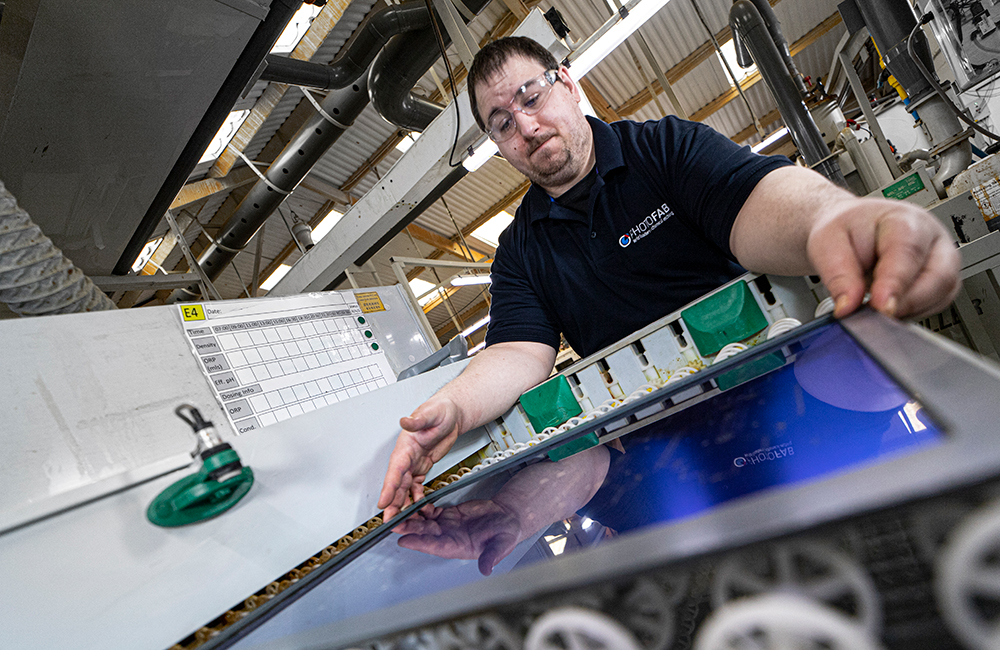
For Volume Production
Continuous investment into the business and the team has delivered the latest advancements in automation technology and processes. Every stage in production has been refined to offer the highest standards with the shortest lead-times possible, from digital tooling, with quick and easy changes to specifications, multi-component designs all on one sheet, through to our multi-sided burr-free metal etching and automated stripping line.
The entire process from quote to delivery has a dedicated point of contact, reinforcing the production process, with full traceability throughout.
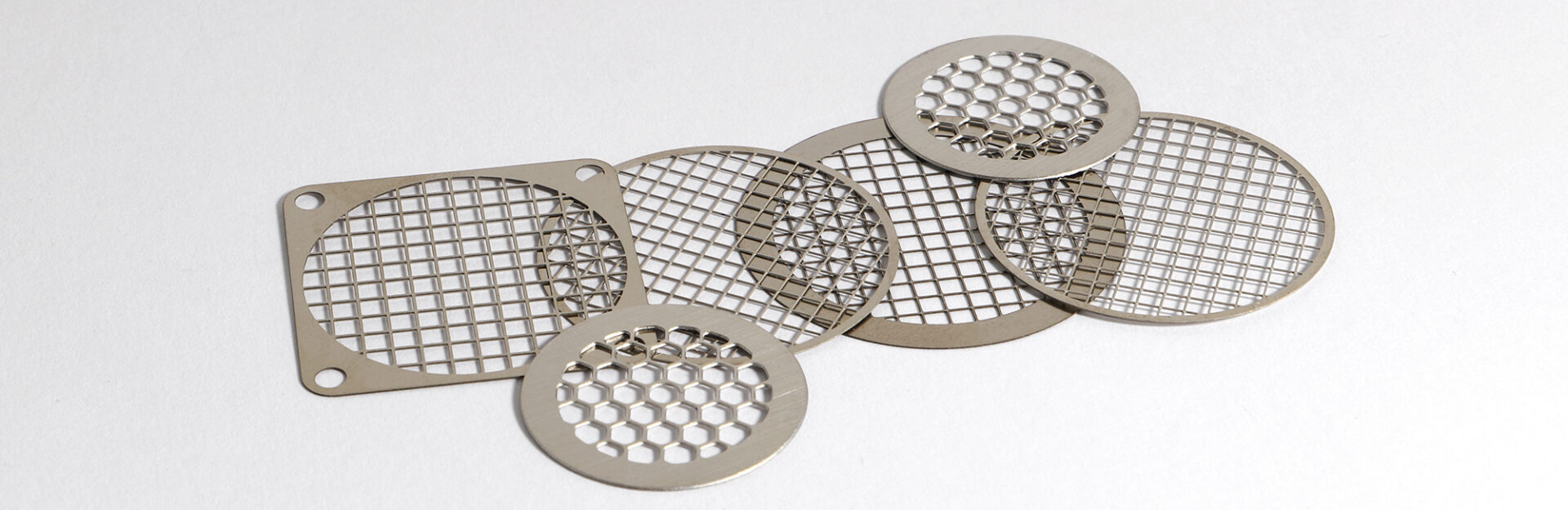
Our Chemical etching tabbing GUIDELINES
In order to further increase the precision of components, we ‘tab’ parts into sheets of metal. Tabs are slivers of metal, that serve to retain parts in sheet form. In other words, once completely etched, the components are not ‘loose’ parts, but instead are held into sheet form using these tabs.
We have devised four different tab styles. These are shown below along with features of each.
Inboard Twist Tabs
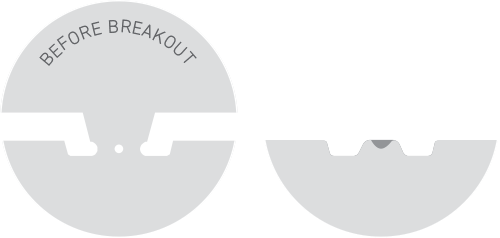
- Full thickness twist tab
- Leaves minimal material loss and no protrusion
Half etch outboard tabs
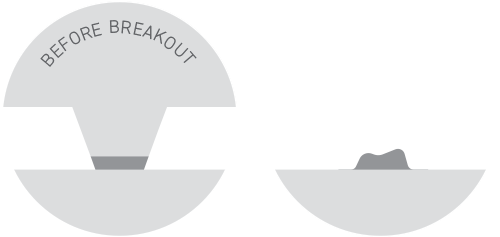
- Used when small protruding witness is acceptable, or when inboard is not an option
- Can be finished on thicker materials to remove protruding witness
Half etch inboard tabs
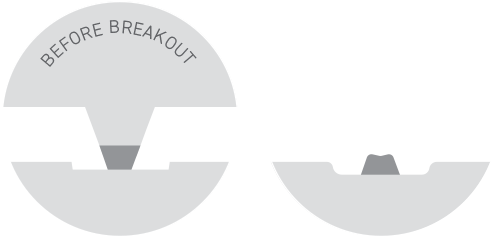
- Half etched break line style
- Used when a small protruding witness is not acceptable
- Breaks slightly inboard or on the component edge leaving no protrusion
Full thickness outboard tabs

- Used when small protruding witness is acceptable – or when inboard is not an option
- Can be finished on thicker materials to remove protruding witness
*1mm is not the dimension of the feature, but is for scale reference only
Tab-less parts can be made if required.
CHEMICAL ETCHING benefits
Discover the advantages of chemical etching.
Low-Cost Tooling
With chemical etching, tooling production doesn’t require the same long-winded, expensive mechanical processes as other methods. Bespoke tooling can be created quickly via CAD – and in the unlikely event of the tooling wearing out, a replacement can be just as quickly created and supplied, free of charge. Contact us for a quote to see how our low-cost tooling can make a huge difference in your production.
Low-Cost Design Changes
The chemical etching process allows the designer to do practical testing at low cost. Rapid prototyping is possible ensuring that cost-effective improvements are easy to implement.
Mixed Graphic Tools for Prototypes
The digital tooling can accommodate several designs, therefore if you are prototyping and wish to trial two or three options on the same sheet of metal, you can. This will greatly reduce the cost of prototyping and reduce lead-times.
HALF-ETCHED FORMING
Forming lines can be half etched into the metal to allow components to be formed by hand.
Mixed Graphic Tools for PROTOTYPE TO FULL PRODUCTION
Chemical etching can be used to make one or a million parts, with the identical tooling used every time. This allows the engineer or designer to develop their concept from prototype to full production quickly and easily, maintaining highly accurate tolerances.
METAL PROPERTIES UNALTERED
Chemical etching carries the unique advantages of leaving the internal structure of the metal unchanged. Neither does it affect the properties of the metal with regard to hardness, grain structure, or ductility of the metal.
Identification Marks
Company logos, part numbers or other identifying marks can easily be etched into the surface during manufacture at no extra cost.
Tabbed-in components
When individual components are tabbed-into sheets, there are benefits of improved tolerances and lower costs.
Metals Suitable for Chemical Etching
The foundation of the component is the metal.
We take great care in the selection of the right metal for the component application. Wherever possible, we use a special photo-etching grade, which is more uniform in thickness and flatter than normal stock. Our engineers and metallurgists will be pleased to advise on the grade of metal suitable for your application.
An extensive range of metals in various degrees of hardness and thickness are held in stock ready to meet a Rapid Delivery service. Metal thickness of 0.005 to 1.5 mm is suitable for through etching, while any thickness of sheet material can be surface etched.
Typically customers are looking at chemical etching aluminum or stainless steel components, but we also have great experience with Nickel and Copper alloys.
The following list of metals is suitable for chemical etching and forming, and many are held in stock. If you don’t see what you need, please telephone us on 01480 226699 or contact us using the form below.

Stainless Steels
Austenitic (301, 302, 304, 316, S526, S527), Martensitic (321, 410, 420), Precipitation Hardened (17/7), Heat Resisting (309, 310)

Other Steels
Mild Steel, Carbon Steel, Tool Steel, Spring Steel, Transil, Losil.

Nickel Alloys
Nichrome, Mu Metal, Nickel Copper (70/30), Inconel, Nickel Brazing Foil.

Nickel/Iron Alloys
Invar, Alloy 42, Kovar, Radio Metal.

Copper
Tough Pitch 101, Oxygen free – High Conductivity.

Copper Alloys
Brass, Phosphor Bronze, Beryllium Copper, Nickel Silver, Ferry Constantan.

Aluminium and Aluminium Alloys

Silver and Alloys
Silver, Silver Alloys, Silver/Copper, Silver/Palladium, Silver Brazing Alloys.
To check the stock of particular metals, or advice on metal suitability, contact us or telephone us on 01480 226699.
The essential guide to getting the most from our Versa-Etch Technology
Reduce costs and optimise prototypes with our Versa-Etch technology.
Our guide details how this flexible chemical etching process allows for cost-effective multiple designs on a single sheet.
DEDICATED engineering
We understand the importance of skilled engineering when designing components and putting them into production. Therefore, we have heavily invested in a dedicated secondary engineering unit, the aim of this is to offer an even greater service and flexibility to our customers.
Originally set up to provide an in-house solution to support the chemical etching division by creating bespoke chemical etching equipment, it has proven so popular with our customers that we are now offering toolroom, forming and finishing as stand-alone services. This means our customers now have access to a new level of flexibility – enjoying the convenience of full-service manufacture or pick and choose services to suit them. It truly is a complete service we offer.
We continue to offer cutting-edge services and outstanding lead times, and we can do so because of continuous investment in our people and our processes, leading to class-leading output and lead times – including our rapid 24 hour turnaround service.
The benefits of
working with us
We are world leaders in the development of photochemical technology to produce intricately shaped components. We have produced over 80,000 different components over the years and are highly regarded for our chemical etching process. Our engineers offer many services that you can find here, and will offer advice to improve the product and reduce the costs.
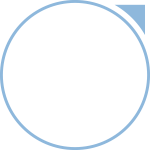
24-hour quotation service
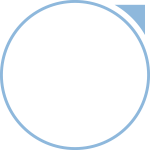
Dedicated account managers
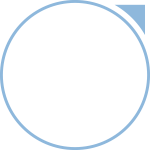
Rapid manufacturing service
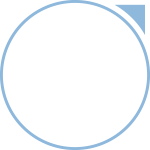
Cost saving stock of uni-tooling
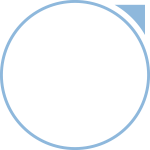
Etched fold lines for tool-free forming
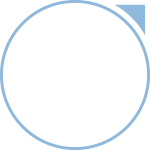
Full manufacturing service and supply chain management
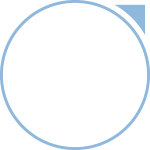
Access to manufacturing and technical advice and expertise
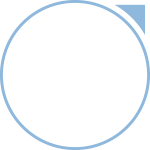
Quality accredited to ISO 9001, ISO 14001, ISO 45001 and SC21 Bronze
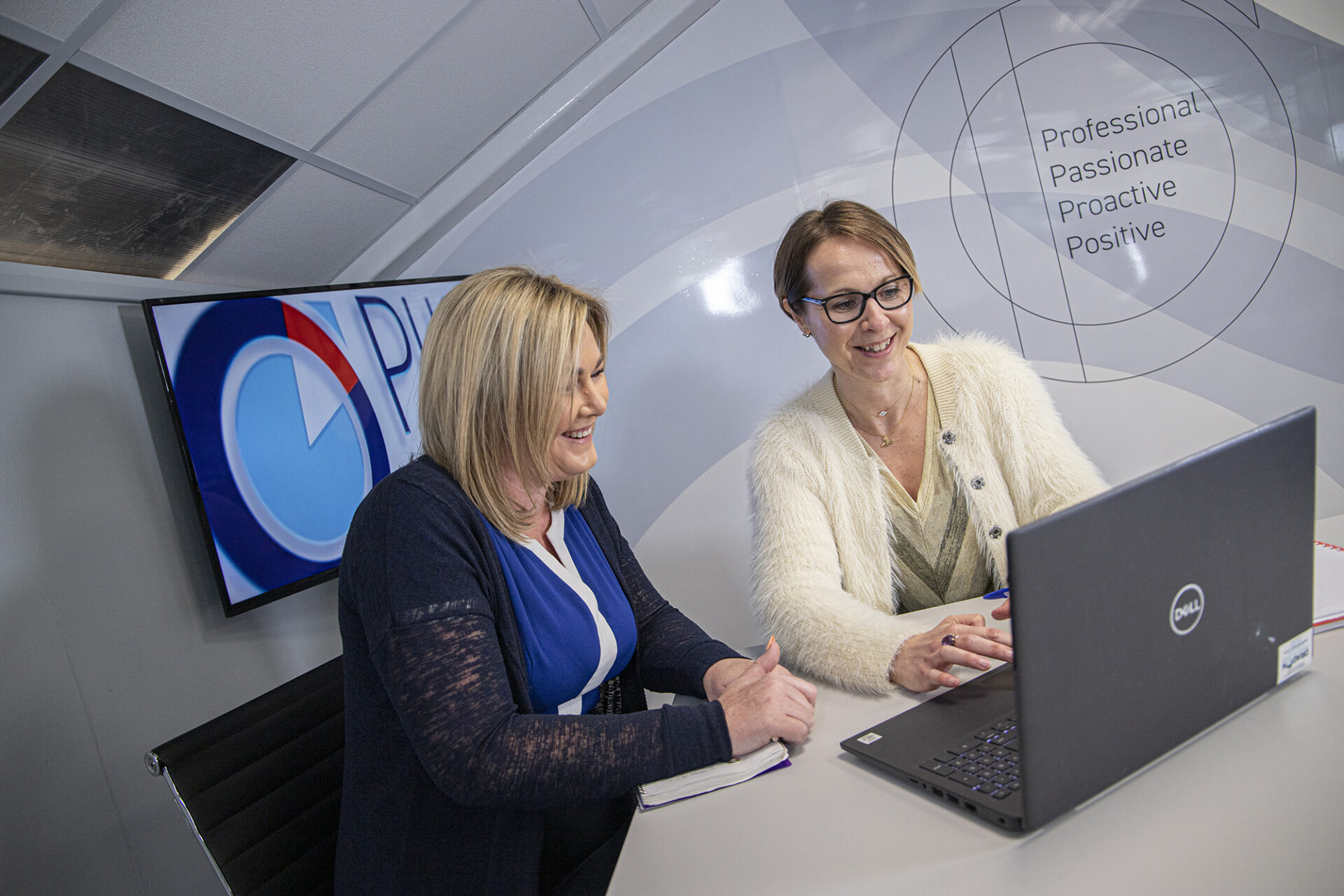
The key difference
One of the key reasons we achieve high levels of customer retention and longevity is the team of dedicated account managers. This ‘single point of contact’ throughout the whole process, ensures a personal service, and pride in the quality and reliability of the entire service.
Customers rely on their dedicated contacts’ understanding and in-depth knowledge of their specific requirements and know the highest standards will always be met using the most efficient and cost-effective methods.
This consistent service is the foundation of our customer loyalty and is maintained throughout every department and every stage of production. Put us to the test for your next project and call one of our account managers on 01480 226699 or use our customer enquiry form.
Value added partnerships
We also have long working relationships with specialist partners for additional finishing services. These services can range from laser-cutting, plating, anodising and heat treatments which can add decorative finishes, prevent corrosion, and further improve durability.
All additional processes are managed closely and delivered with full transparency and traceability.
start your production journey today
If you are looking to find a complete service include dedicated engineering to design and implement your solution, get in touch with us. You’ll be given an account manager who is always on hand to advise and take care of everything for you. Call us on 01480 226699 or contact us now to see how we can add an extra dimension to your manufacturing project.
TAKE A LOOK AT OTHER
SERVICES we offer
To find out how we can help you
Get in touch today
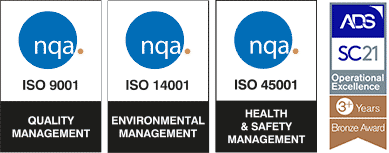